表面轮廓包含哪几种误差
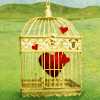
表面轮廓误差通常包括形状误差、位置误差、尺寸误差和表面纹理误差等几种类型。
表面轮廓误差是指在制造和加工过程中,表面轮廓的实际形状与设计要求之间的偏差。这些误差可能会对产品的性能、外观和使用寿命产生重大影响。以下是几种常见的表面轮廓误差类型:
1. 形状误差:
形状误差是指表面轮廓的实际形状与理想形状之间的偏差。这种误差可能表现为表面不平直、曲线不光滑、圆度误差、圆柱度误差等。形状误差的产生可能与机床精度、刀具磨损、材料变形等因素有关。
2. 位置误差:
位置误差是指表面轮廓在空间中的实际位置与设计位置之间的偏差。这种误差可能表现为表面轮廓的偏移、倾斜、扭曲等。位置误差可能由机床安装误差、工件定位不准确、加工过程中振动等因素引起。
3. 尺寸误差:
尺寸误差是指表面轮廓的实际尺寸与设计尺寸之间的偏差。这种误差可能表现为表面轮廓的尺寸过大或过小。尺寸误差可能由加工工具的磨损、机床的精度不足、材料收缩等因素导致。
4. 表面纹理误差:
表面纹理误差是指表面轮廓的纹理粗糙度与设计要求之间的偏差。这种误差可能表现为表面粗糙度过大或过小、纹理不规则等。表面纹理误差不仅影响产品的外观,还可能影响其功能性,如摩擦系数、密封性能等。
为了减少表面轮廓误差,可以采取以下措施:
提高机床精度:选用高精度机床和加工中心,确保加工过程中的稳定性和准确性。
优化刀具参数:根据加工材料和工件要求,选择合适的刀具和切削参数,减少刀具磨损和加工变形。
控制加工环境:保持加工环境的稳定,减少温度、湿度等外界因素对加工精度的影响。
采用先进的检测技术:利用高精度测量仪器,对表面轮廓进行实时检测和反馈,及时调整加工参数。
严格质量控制:加强生产过程中的质量控制,确保每个环节符合设计要求。
总之,表面轮廓误差是影响产品质量的重要因素。通过采取有效措施,可以降低误差,提高产品的精度和性能。