轴承支点距离怎么确定
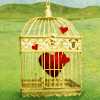
轴承支点距离的确定通常基于设备的设计要求、轴承的类型和尺寸、以及预期的负载和转速。
轴承支点距离的确定是机械设备设计中的一个关键环节,它直接影响到轴承的工作性能和设备的整体稳定性。以下是确定轴承支点距离的几个主要考虑因素和方法:
1. 设备设计要求:
首先需要参考设备的设计图纸和说明书,了解设备的整体布局和轴承的使用位置。
设备的设计要求会明确指出轴承的支点距离,以确保设备在运行过程中的平衡和稳定。
2. 轴承的类型和尺寸:
不同类型的轴承(如深沟球轴承、圆柱滚子轴承、角接触球轴承等)有其特定的安装和使用要求。
轴承的尺寸也会影响支点距离的选择,例如,较大的轴承可能需要更远的支点距离以承受更大的负载。
3. 预期的负载和转速:
轴承支点距离的选择应能保证轴承在承受预期负载时不会出现过载。
高转速的设备可能需要更小的支点距离以减少振动和噪音,同时确保轴承的冷却效果。
4. 热膨胀和轴向位移:
考虑到工作温度的变化,轴承和轴可能会有一定的热膨胀,这需要在支点距离的设计中预留一定的空间。
同时,轴向位移也需要在支点距离中考虑,以避免因轴向位移导致的轴承过早磨损。
5. 力学计算和模拟:
使用力学计算软件(如ANSYS、ABAQUS等)对轴承进行受力分析,可以更精确地确定支点距离。
通过模拟轴承在不同负载和转速下的工作状态,可以优化支点距离,确保轴承在最佳状态下工作。
6. 安全系数:
在确定支点距离时,应考虑一定的安全系数,以应对突发负载或异常情况。
具体确定轴承支点距离的方法如下:
计算轴承的额定载荷和实际载荷,确保支点距离能够承受实际负载。
根据轴承的类型和尺寸,查阅相关技术手册或标准,确定推荐的支点距离范围。
结合设备的具体工作条件,如温度、转速等,对推荐的支点距离进行适当调整。
最终确定的支点距离应通过实验验证,确保在实际工作中能够满足设计要求。
总之,轴承支点距离的确定是一个综合考虑多方面因素的过程,需要设计人员具备丰富的经验和专业知识。