精益生产现场管理工作怎么做的
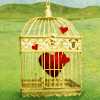
精益生产现场管理工作是一个系统工程,它要求企业从思想观念、组织结构、流程设计、人员培训等方面进行全面优化。以下是精益生产现场管理工作的具体做法:
1. 确立精益理念:
企业领导层首先要树立精益生产的理念,认识到精益生产对于提升企业竞争力的重大意义。
通过内部培训和外部交流,使全体员工了解精益生产的核心理念,如“五个为什么”、“价值流分析”等。
2. 现场5S管理:
推行5S管理(整理、整顿、清扫、清洁、素养),打造整洁、有序的工作环境。
定期检查和维持5S管理的有效性,确保工作现场无杂物、无污染、无浪费。
3. 价值流分析:
对生产流程进行全面的价值流分析,识别并消除非增值活动。
通过优化流程,减少生产周期,提高生产效率。
4. 持续改进:
建立持续改进机制,鼓励员工提出改进建议,并对合理的建议给予奖励。
定期回顾和评估改进措施的实施效果,确保持续改进的持续性和有效性。
5. 减少浪费:
识别并减少七大浪费(过度生产、等待、运输、库存、加工、过度加工和缺陷)。
通过改进生产设备、优化生产计划、提高员工技能等方式减少浪费。
6. 标准化作业:
建立标准化的作业流程,确保每个环节都按照既定标准进行操作。
定期对标准进行审查和更新,以适应市场变化和技术进步。
7. 人员培训:
加强对员工的培训,提高员工的技能和素养。
培养员工的团队协作精神和主人翁意识,使员工能够积极参与精益生产活动。
8. 可视化管理:
在生产现场设置看板,将生产进度、质量状况等信息可视化,便于管理人员和员工及时掌握生产动态。
通过可视化管理,提高生产透明度,便于及时发现和解决问题。
9. 质量管理体系:
建立完善的质量管理体系,确保产品质量符合要求。
通过质量改进活动,降低不良品率,提高顾客满意度。
10. 跨部门协作:
加强跨部门沟通与协作,打破部门壁垒,实现资源整合和协同效应。
通过跨部门协作,提高整体生产效率和市场响应速度。
总之,精益生产现场管理工作需要企业从多个层面进行系统性的优化,通过持续改进和消除浪费,实现生产过程的优化和效率的提升。