高耐热模具钢及其热处理工艺
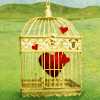
高耐热模具钢及其热处理工艺的研究对于提高模具使用寿命和性能至关重要。
高耐热模具钢是一种在高温环境下仍能保持良好机械性能的合金钢,广泛应用于塑料、金属成型等行业。其优异的性能主要源于其特殊的化学成分和热处理工艺。
首先,高耐热模具钢的化学成分设计是其关键。通常,这类钢种含有较高的铬、镍、钼等合金元素,这些元素可以提高钢的耐热性、抗氧化性和耐磨性。例如,铬可以提高钢的抗氧化能力,而钼则有助于提高钢的热稳定性。
其次,热处理工艺对高耐热模具钢的性能影响极大。常见的热处理工艺包括退火、淬火和回火。
1. 退火:退火是高耐热模具钢生产的第一步,目的是消除钢中存在的应力,提高材料的塑性和韧性。退火温度通常在800-900摄氏度之间,保温时间为1-2小时。
2. 淬火:淬火是将退火后的钢材快速冷却至室温,以获得高硬度和耐磨性。淬火温度根据钢种不同而有所差异,一般在1050-1200摄氏度之间。淬火后,钢材需要立即进行回火处理。
3. 回火:回火是淬火后的后续处理,目的是消除淬火应力,提高材料的韧性。回火温度通常在500-600摄氏度之间,保温时间为1-2小时。
在实际生产中,为了进一步提高高耐热模具钢的性能,还可以采用以下几种特殊的热处理工艺:
真空热处理:在真空环境下进行热处理,可以有效去除钢中的气体和非金属夹杂物,提高钢的纯净度和性能。
预处理:在淬火前对钢材进行预处理,如表面硬化处理,可以提高钢材的耐磨性和使用寿命。
低温热处理:在较低温度下进行热处理,可以降低钢材的脆性,提高其韧性。
总之,高耐热模具钢及其热处理工艺的研究对于提高模具使用寿命和性能具有重要意义。通过合理设计和优化热处理工艺,可以有效提高高耐热模具钢的性能,满足各类工业生产的需要。