工厂里面的八大浪费心得体会
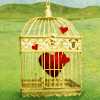
通过工厂内部八大浪费现象的识别与优化,可以有效提升生产效率,降低成本,增强企业竞争力。
在工厂的生产过程中,浪费现象无处不在,它们不仅消耗了企业的大量资源,也降低了生产效率。以下是工厂内部常见的八大浪费现象及心得体会:
1. 材料浪费:
材料浪费是工厂中最常见的浪费形式之一。为了减少材料浪费,企业应加强材料管理,合理规划库存,采用精益生产方式,精确计算所需材料,减少过剩和短缺。
心得体会:通过实施ERP系统,实时监控材料消耗,优化生产计划,可以有效降低材料浪费。
2. 生产过程浪费:
生产过程中,由于设备故障、操作不当等原因,导致生产效率低下。对此,企业应定期维护设备,提高员工操作技能,优化生产流程。
心得体会:加强员工培训,提高设备维护意识,有助于减少生产过程中的浪费。
3. 等待浪费:
等待是生产过程中的一个重要环节,过长的等待时间会降低生产效率。企业可以通过优化生产计划,减少生产环节间的等待时间。
心得体会:采用看板管理系统,实现生产信息的实时传递,可以减少等待浪费。
4. 运输浪费:
不必要的运输会增加成本,降低效率。企业应优化运输路线,减少运输次数,提高运输效率。
心得体会:合理规划运输计划,采用集装化运输,可以降低运输浪费。
5. 过度加工浪费:
过度加工是指生产过程中超出客户需求的部分。企业应明确客户需求,避免过度加工。
心得体会:加强与客户的沟通,了解客户需求,有助于减少过度加工浪费。
6. 库存浪费:
库存过高会增加存储成本,降低资金周转率。企业应合理控制库存,避免库存积压。
心得体会:实施库存管理系统,实时监控库存情况,有助于减少库存浪费。
7. 缺陷浪费:
缺陷产品会增加返工、维修等成本。企业应加强质量管理,减少缺陷产品。
心得体会:实施全面质量管理(TQM),提高员工质量意识,有助于降低缺陷浪费。
8. 能力浪费:
人力资源、设备资源等未能充分利用会导致能力浪费。企业应优化资源配置,提高资源利用率。
心得体会:通过绩效考核,激发员工潜能,提高设备使用效率,有助于减少能力浪费。
总之,通过识别和优化工厂内部的八大浪费现象,企业可以降低生产成本,提高生产效率,增强市场竞争力。在实际操作中,企业应根据自身情况,采取针对性的措施,实现精益生产。