线切割切削液怎么处理
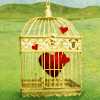
线切割切削液的处理方法主要包括以下几个步骤和注意事项:
1. 收集与沉淀:
首先,需要定期收集使用过的切削液,避免切削液中的金属屑和杂质积累过多,影响切削效果和设备的使用寿命。收集后,可以使用沉淀法去除其中的大颗粒杂质,如金属屑和油泥。
2. 过滤:
通过使用过滤器对切削液进行过滤,可以进一步去除细小的金属颗粒和悬浮物。根据切削液的污染程度,可以选择不同精度的过滤器,如粗滤、中滤和精滤。
3. 化学处理:
对于含有油性物质的切削液,可以使用化学试剂如破乳剂进行乳化油的分解,使其易于分离。此外,还可以添加杀菌剂和防锈剂,以抑制细菌生长和防止切削液变质。
4. 再生处理:
对于污染严重的切削液,可以考虑采用再生处理技术,如离心分离、蒸馏、吸附等,以恢复切削液的性能。再生处理后,切削液可能需要重新添加添加剂以达到理想的使用状态。
5. 废弃处理:
对于无法再生利用的切削液,应按照环保法规进行妥善处理,通常包括送到专业的废弃物处理中心,进行无害化处理,如焚烧、填埋或化学中和。
6. 日常维护:
保持切削液的清洁是延长其使用寿命的关键。定期检查切削液的pH值、浓度和颜色,确保其在适宜的范围内。同时,定期更换新液,以补充消耗的添加剂和保证切削液的性能。
7. 环保意识:
在选择切削液时,优先考虑环保型产品,如水基切削液,它们的生物降解性较好,对环境影响较小。同时,减少切削液的使用量,提高循环利用效率,也是降低环境污染的有效途径。
1、线切割切削液的成分
线切割切削液的成分通常包括以下几类:
1. 基础液:水基切削液主要由去离子水或蒸馏水组成,油基切削液则以矿物油或合成油为主。
2. 极压添加剂:如硫化油、氯化石蜡等,用于在切削过程中形成保护膜,降低切削温度,提高加工精度和刀具寿命。
3. 防锈剂:如亚硝酸钠、磷酸盐等,防止加工后的工件生锈。
4. 表面活性剂:如脂肪醇、磺酸盐等,降低液体的表面张力,提高冷却和润滑效果。
5. 杀菌剂:如季铵盐、酚类化合物等,防止细菌和霉菌滋生,延长切削液的使用寿命。
6. pH调节剂:如氢氧化钠、磷酸等,维持切削液的pH值稳定,确保其性能稳定。
7. 抗泡沫剂:如硅油、聚醚等,防止切削液在使用过程中产生过多泡沫,影响加工效果。
2、线切割切削液的危害
线切割切削液在使用过程中可能产生的危害主要包括:
1. 环境影响:废弃的切削液如果不妥善处理,可能会对土壤和水源造成污染,特别是油基切削液,其生物降解性较差。
2. 健康风险:部分切削液含有有害化学物质,如甲醛、苯等,长期接触可能对操作人员的皮肤和呼吸系统造成刺激,甚至引发职业病。
3. 火灾隐患:油基切削液易燃,如果管理不当,可能引发火灾。
4. 设备腐蚀:切削液中的酸碱物质可能对设备的金属部件产生腐蚀,影响设备的使用寿命。
通过科学的处理方法和日常维护,可以有效降低线切割切削液对环境和健康的潜在影响,同时提高切削液的使用效率和设备的加工性能。