铝合金厂挤压工艺
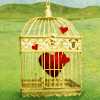
铝合金厂挤压工艺是一种通过施加压力使铝棒在模具中变形,从而得到所需形状和尺寸的加工方法。
铝合金厂挤压工艺是铝材加工中的重要环节,广泛应用于建筑、交通运输、电子、航天航空等领域。该工艺的基本流程如下:
1. 准备阶段:首先,选择合适的铝棒作为坯料,这些铝棒可以是实心的也可以是空心的,通常是圆柱体形状。这些铝棒通常是通过铸造、锻造或粉末冶金等方法成型。
2. 加热:在挤压前,铝棒需要加热到适当的温度,以增加其塑性和降低变形抗力。加热温度通常在350°C到500°C之间。
3. 挤压:加热后的铝棒被送入挤压机,挤压机对铝棒施加强大的压力,迫使铝棒通过模具的模孔。在这个过程中,铝棒发生定向塑性变形,形成所需的断面形状和尺寸。
4. 冷却与定形:挤压后的铝材在挤压筒内迅速冷却,以固定其形状。冷却方式可以是水冷、风冷或空气淬火。
5. 后续处理:根据产品要求,铝材可能需要进行表面处理(如阳极氧化、涂漆等)、机械加工(如CNC加工、冲压等)或其他特殊处理。
铝合金挤压工艺的关键工艺参数包括挤压比(挤压前后截面积之比)、模具设计、加热温度、挤压速度等。挤压比和模具设计对产品的尺寸精度、表面质量和力学性能有重要影响。
近年来,随着技术的进步,铝合金挤压工艺也不断创新。例如,采用分流板技术可以降低分流桥的承压力,提高模具寿命;而在模具设计方面,也出现了许多创新,如多级分流通道设计,以优化铝材流动和减少模孔磨损。
铝合金挤压工艺具有生产效率高、设备投资少、经济效益好等优点,是铝材加工中不可或缺的工艺之一。