内浇口缩孔解决办法
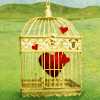
通过优化设计、调整工艺参数和采用适当的材料处理方法可以有效解决内浇口缩孔问题。
内浇口缩孔是指在注塑过程中,由于冷却速度不均匀或者材料流动性不足,导致浇口区域形成的空洞或凹陷。这种现象不仅影响产品的外观质量,还可能影响产品的力学性能和使用寿命。以下是一些解决内浇口缩孔问题的方法:
1. 优化设计:
浇口位置:选择合适的浇口位置,避免在产品的薄壁或高应力集中区域设置浇口。
浇口类型:根据产品的形状和尺寸,选择合适的浇口类型,如点浇口、扇形浇口或侧浇口,以改善材料的流动性和冷却均匀性。
浇口尺寸:合理设计浇口尺寸,确保材料能够充分流动并填充模具型腔。
2. 调整工艺参数:
注射速度:适当调整注射速度,避免过快或过慢的注射速度导致材料流动不均。
压力控制:保持适当的注射压力,确保材料能够均匀地填充型腔。
冷却时间:调整冷却时间,确保产品在不同区域的冷却速度一致。
3. 材料处理:
材料选择:选择适合注塑的材料,避免使用容易产生缩孔的树脂。
预塑化:确保材料在注射前充分预塑化,提高材料的流动性。
添加剂:在材料中添加适量的流动改性剂或成核剂,改善材料的流动性和冷却性能。
4. 模具设计:
冷却系统:优化模具的冷却系统,确保模具各部分的温度分布均匀。
排气系统:设计合理的排气系统,防止气体在型腔内积聚导致缩孔。
5. 其他措施:
预热:在注塑前对模具进行预热,减少模具与材料之间的温差。
后处理:对产品进行适当的后处理,如热处理或机械加工,以改善其性能。
通过上述方法,可以有效地解决内浇口缩孔问题,提高注塑产品的质量和生产效率。在实际操作中,需要根据具体的产品和材料特性,综合考虑各种因素,选择最合适的解决方案。