铸件有缩孔和缩松的主要原因
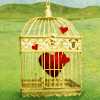
铸件产生缩孔和缩松的主要原因是冷却过程中的收缩不均匀和凝固过程中的体积收缩。
铸件在铸造过程中,由于金属液在凝固过程中会发生体积收缩,这种收缩会导致铸件内部产生空隙,从而形成缩孔和缩松。以下是铸件产生缩孔和缩松的主要原因:
1. 冷却速度不均匀:在铸造过程中,铸件各部分的冷却速度不同,导致局部区域收缩速度较快,而其他部分收缩速度较慢。这种不均匀的收缩会在铸件内部产生应力,当应力超过金属的强度极限时,就会在铸件中形成缩孔。
2. 铸件结构设计:铸件的结构设计不合理,如壁厚不均、形状复杂、有锐角或薄壁部分,这些都会导致冷却速度差异,从而引起缩孔和缩松。例如,铸件厚壁部分冷却速度慢,薄壁部分冷却速度快,使得厚壁部分在凝固时收缩较大,容易形成缩孔。
3. 金属液的纯净度:金属液中的杂质和夹杂物会影响其凝固过程中的收缩性能。杂质和夹杂物在凝固时可能会阻碍金属的正常收缩,导致缩孔和缩松的产生。
4. 铸造工艺:铸造工艺参数如浇注温度、浇注速度、冷却速度等对铸件的收缩有重要影响。不当的浇注温度和速度会导致金属液在凝固过程中的收缩不均匀,从而形成缩孔和缩松。
5. 凝固组织:金属液的凝固组织对缩孔和缩松的形成也有影响。凝固组织不致密,如存在大量的晶界孔洞,会使得铸件在收缩时容易产生缩孔和缩松。
为了减少或消除铸件中的缩孔和缩松,可以采取以下措施:
优化铸件结构设计,减少壁厚不均和形状复杂的设计。
提高金属液的纯净度,减少夹杂物和杂质。
控制铸造工艺参数,如浇注温度、浇注速度和冷却速度。
在铸件设计时考虑设置冒口和冷铁,以促进金属液的充分凝固和收缩。
使用热处理方法来调整铸件的收缩性能,如退火处理。
通过上述措施,可以有效减少铸件中缩孔和缩松的产生,提高铸件的质量。