注塑件缩水的原因
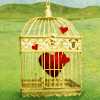
注塑件缩水的原因主要包括材料性能、模具设计、加工工艺、环境因素等方面。
注塑件缩水是指注塑成型的塑料制品在冷却过程中,其尺寸小于理论尺寸的现象。这种现象不仅影响产品的外观质量,还可能影响其使用性能。以下是注塑件缩水的主要原因:
1. 材料性能:注塑材料的熔体流动性和热稳定性是影响注塑件缩水的主要因素。熔体流动性差会导致填充不足,从而产生缩水;热稳定性差则可能导致材料在冷却过程中收缩过大。
2. 模具设计:模具设计不合理是导致注塑件缩水的重要原因。主要包括以下方面:
模具温度分布不均匀:模具温度过高或过低都会影响塑料的冷却速度,导致注塑件缩水。
模具型腔和流道设计不合理:型腔和流道设计不合理会导致熔体填充不充分,产生缩水。
冷却系统设计不合理:冷却系统设计不合理会导致冷却速度不均匀,从而产生缩水。
3. 加工工艺:加工工艺对注塑件缩水的影响主要体现在以下几个方面:
注塑压力和速度:注塑压力和速度过高或过低都会影响注塑件的密度和尺寸稳定性。
注塑温度:注塑温度过高或过低都会影响塑料的熔体流动性和热稳定性,进而影响注塑件的缩水程度。
注塑时间:注塑时间过长或过短都会影响注塑件的冷却速度和尺寸稳定性。
4. 环境因素:环境因素主要包括温度、湿度和气压等。温度过高或过低、湿度过大或过小都会影响注塑件的冷却速度和尺寸稳定性。
为了减少注塑件缩水,可以采取以下措施:
选择合适的注塑材料,提高其熔体流动性和热稳定性;
优化模具设计,确保模具温度分布均匀,型腔和流道设计合理;
优化加工工艺,控制注塑压力、速度和温度,确保注塑件的密度和尺寸稳定性;
控制生产环境,保持适宜的温度、湿度和气压。
总之,注塑件缩水是一个复杂的问题,涉及多个方面的因素。通过合理选择材料、优化模具设计、加工工艺和环境控制,可以有效减少注塑件缩水现象。