精益生产的工位布局
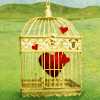
精益生产工位布局应遵循高效、便捷、灵活的原则,以减少物料搬运、降低在制品库存、提高员工操作便利性为目标。
精益生产的工位布局是精益管理的重要组成部分,它直接影响到生产效率、产品质量和成本控制。以下是对精益生产工位布局的详细阐述:
1. 高效原则:工位布局的首要目标是提高生产效率。这包括减少物料的搬运距离、减少生产过程中的等待时间、提高设备利用率等。具体措施如下:
直线布局:将生产设备沿生产线排列成直线,使物料流和生产流程尽可能顺畅。
U型布局:适用于批量生产,将加工设备围绕物料存储区域排列成U型,减少物料搬运。
S型布局:适用于多品种小批量生产,通过S型布局,可以实现设备之间的灵活转换。
2. 便捷原则:工位布局应考虑员工的操作便利性,减少员工的劳动强度,提高工作效率。具体措施如下:
操作空间:确保每个工位有足够的空间供员工操作,避免拥挤。
工具与材料放置:将常用的工具和材料放置在员工易于取用的位置,减少寻找和等待时间。
站立与坐姿设计:根据工作性质,设计合适的站立或坐姿工作台,减少疲劳。
3. 灵活原则:精益生产要求工位布局具有灵活性,以适应市场需求的变化和生产计划的调整。具体措施如下:
模块化设计:将生产设备设计成模块化,便于快速调整和重组。
多功能工位:设计多功能工位,使同一工位能够适应不同的生产任务。
可移动设备:使用可移动的设备,以便根据生产需求调整布局。
4. 质量控制:工位布局还应考虑质量控制因素,确保产品质量。具体措施如下:
检验站设置:在关键工位设置检验站,及时发现并解决问题。
防错设计:在工位布局中融入防错设计,减少人为错误。
5. 持续改进:工位布局不是一成不变的,应根据生产实际情况和精益管理的目标,不断进行改进。具体措施如下:
数据收集与分析:定期收集生产数据,分析工位布局的优缺点。
员工参与:鼓励员工提出改进建议,共同优化工位布局。
总之,精益生产的工位布局需要综合考虑效率、便捷、灵活和质量控制等多方面因素,通过不断优化和改进,实现生产过程的持续优化。