加工中心铣刀片为什么不耐用
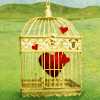
加工中心铣刀片不耐用可能是由多种因素造成的,包括材料选择、制造工艺、使用条件以及维护保养不当等。
加工中心铣刀片是加工中心设备中不可或缺的切削工具,其耐用性直接影响到加工效率和成本。以下是导致加工中心铣刀片不耐用的一些主要原因:
1. 材料选择不当:铣刀片的材料是决定其耐用性的关键因素。如果选择了不适合特定加工材料的刀具材料,如硬度不足或者耐磨性差,那么铣刀片在加工过程中容易磨损,从而降低耐用性。
2. 制造工艺问题:铣刀片的制造工艺包括刀片的设计、热处理、涂层等环节。如果这些环节中存在缺陷,比如刀片设计不合理、热处理不当或涂层质量不佳,都可能导致铣刀片在使用中容易损坏。
3. 使用条件不当:铣刀片的使用条件,如切削速度、进给量、切削深度等,都会对刀具的耐用性产生影响。如果切削参数设置不当,超出刀具的承受范围,就会加速刀具的磨损。
4. 维护保养不充分:铣刀片在使用过程中需要定期进行清洁、润滑和检查。如果维护保养工作不到位,如不及时清除切削液中的金属屑和冷却液中的污染物,会导致铣刀片表面受损,从而影响其耐用性。
5. 切削液选择不当:切削液在切削过程中起到冷却、润滑和清洗的作用。如果切削液选择不当,比如粘度不适合或含有对刀具有害的成分,也会加速铣刀片的磨损。
6. 加工中心机床精度问题:加工中心机床的精度直接影响到铣刀片的切削效果。如果机床精度不足,会导致刀具与工件的接触不良,从而增加铣刀片的磨损。
为了提高加工中心铣刀片的耐用性,可以采取以下措施:
选择合适的铣刀片材料,确保其硬度和耐磨性满足加工需求。
严格控制铣刀片的制造工艺,确保刀片的质量。
合理设置切削参数,避免超出铣刀片的承受范围。
定期进行铣刀片的维护保养,确保其清洁和润滑。
使用合适的切削液,并定期更换以保持其性能。
定期检查机床的精度,确保加工过程中的稳定性。
通过这些措施,可以有效提高加工中心铣刀片的耐用性,降低加工成本,提高生产效率。