如何确定切削用量大小
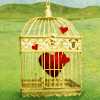
确定切削用量大小需要综合考虑工件材料、刀具材料、机床性能、加工精度要求以及经济性等因素。
切削用量的大小直接影响到切削过程的效率、工件加工质量和成本。以下是一些确定切削用量大小的步骤和方法:
1. 工件材料分析:
材料的硬度、韧性、热导率等物理性质都会影响切削用量。例如,硬度高的材料需要较小的切削深度和进给量,以避免刀具磨损过快。
2. 刀具材料选择:
刀具材料的选择也很关键。高速钢、硬质合金、陶瓷等不同材料的刀具适合不同的切削条件。例如,硬质合金刀具适用于高速切削。
3. 机床性能:
机床的刚性和动力性能会影响切削用量的选择。机床刚度越高,允许的切削深度和进给量越大。
4. 加工精度要求:
加工精度要求高的工件需要较小的切削深度和进给量,以及较高的切削速度,以确保表面质量。
5. 切削液使用:
切削液可以降低切削温度,减少刀具磨损,从而允许使用较高的切削速度和切削深度。
6. 经济性考虑:
经济性是切削用量选择时不可忽视的因素。过高的切削用量可能导致刀具快速磨损,增加更换频率和成本。
具体确定切削用量的步骤如下:
初步估计:根据经验公式和参考数据初步确定切削深度、进给量和切削速度的范围。
切削试验:在实际机床上进行切削试验,根据试验结果调整切削用量。
数据分析:对试验数据进行统计分析,确定最佳的切削用量组合。
验证和调整:在实际生产中验证切削效果,根据实际情况进行必要的调整。
总之,确定切削用量大小是一个系统工程,需要综合考虑多方面因素,通过试验和经验积累,找到最适合的切削条件。