注塑pp材料为什么有时粘模严重
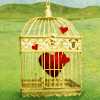
注塑PP材料有时粘模严重,主要是由于材料特性、工艺参数、模具设计以及环境因素等多种原因共同作用的结果。
注塑PP材料粘模是一个常见的注塑缺陷,其原因可以从以下几个方面进行分析:
1. 材料因素:
熔融指数(MI):PP材料的熔融指数较低时,熔体流动性差,容易在模具表面形成粘附。
润滑性:PP材料的润滑性不佳,使得材料在模具表面难以滑动,从而加剧粘模现象。
2. 工艺参数:
温度控制:注塑温度过高或过低都会影响PP材料的流动性,过高的温度可能导致材料过度软化,从而粘模;而过低的温度则会使材料流动性差。
注射压力:注射压力不足可能导致材料在模具内分布不均,增加粘模风险。
冷却速度:冷却速度过快可能导致材料收缩不均匀,形成应力集中,从而引发粘模。
3. 模具设计:
模具表面粗糙度:模具表面粗糙度增加,会增大材料与模具间的摩擦力,导致粘模。
模具排气不良:模具排气不畅,会导致材料在充模过程中产生气泡,影响材料流动,增加粘模的可能性。
4. 环境因素:
湿度:高湿度环境可能导致PP材料吸湿,降低其熔融指数,从而增加粘模风险。
材料存放:PP材料存放不当,如长时间暴露在阳光下或存放环境温度过高,可能导致材料性能下降,增加粘模。
为了解决注塑PP材料粘模问题,可以从以下几个方面进行改进:
选择合适的PP材料,提高其熔融指数和润滑性。
调整注塑工艺参数,如温度、压力和冷却速度等,以优化材料流动和冷却。
改进模具设计,提高模具表面光洁度和排气效率。
加强材料存放管理,确保材料性能稳定。