简单说明如何确定切削用量
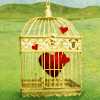
确定切削用量需要综合考虑机床性能、刀具材料、工件材料、加工精度要求等因素,通过实验和经验进行合理选择。
切削用量是指在金属切削过程中,切削速度、进给量和切削深度的总称。这三个参数直接影响到切削过程的效率、加工质量以及机床刀具的磨损情况。以下是如何确定切削用量的步骤和注意事项:
1. 了解机床性能:
首先,需要熟悉所使用的机床的性能参数,如主轴转速、进给机构的最大进给量等。这些参数将限制切削用量的选择范围。
2. 分析刀具材料:
刀具材料的选择对切削用量有重要影响。高速钢刀具适合中低切削速度,而硬质合金刀具则适用于较高的切削速度。刀具的耐用性和硬度也是考虑因素。
3. 工件材料:
不同的工件材料具有不同的切削性能。例如,钢的切削性能通常优于铸铁,而铸铁的切削性能又优于铝和铜。工件的材料性质将决定切削速度和进给量的选择。
4. 加工精度要求:
根据加工精度要求,选择合适的切削深度。高精度加工时,切削深度应较小,以保证加工表面的光洁度和尺寸精度。
5. 实验验证:
在确定切削用量时,可以通过实验来验证所选参数的合理性。通过改变切削速度、进给量和切削深度,观察切削效果,如切屑形态、表面质量、刀具磨损情况等。
6. 参考经验:
切削用量的选择还需要参考相关标准和经验数据。例如,机械加工手册、行业规范等都会提供一定的参考值。
7. 安全因素:
在确定切削用量时,还需考虑操作人员的安全。避免过大的切削用量导致机床或刀具损坏,造成安全事故。
8. 持续优化:
随着切削工艺的不断发展,切削用量的确定也需要不断优化。通过实际加工过程中的经验积累,逐步调整切削用量,以实现更高的加工效率和更好的加工质量。
总之,确定切削用量是一个系统工程,需要综合考虑多方面因素,通过实验和经验不断调整和优化。