无缝钢管的主要生产设备及工艺流程
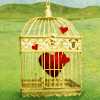
无缝钢管是一种重要的流体输送管道,其主要生产设备及工艺流程如下:
1. 管坯准备:首先选用合适的管坯,一般为圆形或方形,材质多为碳钢或不锈钢。
2. 管坯加热:将管坯加热至一定温度,使其具有良好的塑性,以便于后续的加工。
3. 穿孔:在管坯的一端穿一个孔,使管坯形成管状。
4. 打头:在管坯的另一端打一个头,形成封闭的管状。
5. 退火:将管坯加热至一定温度,然后缓慢冷却,以消除内应力,提高管材的韧性。
6. 酸洗:用酸液清洗管材表面,去除氧化皮、锈蚀等杂质。
7. 涂油(镀铜):在管材表面涂上一层防锈油或镀上一层铜,以防止管材生锈。
8. 多道次冷拔(冷轧):将管材通过多道次冷拔(冷轧)设备,使其直径逐渐减小,以达到所需的尺寸。
9. 热处理:将管材加热至一定温度,然后缓慢冷却,以提高管材的强度和硬度。
10. 矫直:将热处理后的管材进行矫直,使其表面平整。
11. 水压试验(探伤):将管材进行水压试验,以检测其内部是否存在裂纹、砂眼等缺陷。
12. 包装:将合格的管材进行包装,以便于运输和储存。
以上是无缝钢管的主要生产设备及工艺流程,通过这些工艺,可以生产出高质量的无缝钢管,满足各种流体输送需求。