数控机床对刀间隙怎么处理
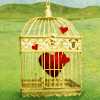
数控机床在对刀过程中,由于刀具与工件之间的间隙问题,可能会影响加工精度和加工质量。以下是一些处理数控机床对刀间隙的方法:
1. 调整对刀参数:
刀具长度补偿:在数控程序中设置刀具长度补偿值,使刀具实际工作长度与理论长度相匹配,从而减少间隙。
刀具半径补偿:通过设置刀具半径补偿值,调整刀具的切削轨迹,使刀具实际切削路径与编程路径一致,减少因刀具半径误差导致的间隙。
2. 优化刀具选择:
选择合适的刀具类型和尺寸,确保刀具与工件的良好匹配,减少因刀具过大或过小导致的间隙。
定期检查刀具的磨损情况,及时更换磨损刀具,以保证加工精度。
3. 改进机床精度:
定期对机床进行校准和维护,确保机床的几何精度和运动精度。
检查机床导轨的磨损情况,及时更换或修复,以提高机床的定位精度。
4. 调整对刀方法:
采用自动对刀系统,通过传感器自动测量刀具尺寸和位置,减少人工对刀误差。
在对刀时,尽量使刀具与工件接触面垂直,减少因角度偏差导致的间隙。
5. 优化加工工艺:
在加工过程中,合理调整切削参数,如切削速度、进给量等,以减少切削力对刀具的影响。
采用预紧刀柄技术,提高刀具的稳定性,减少因刀具振动导致的间隙。
6. 使用补偿软件:
利用数控机床的补偿软件,对刀具间隙进行实时监控和调整,确保加工精度。
7. 定期检查和调整:
在加工过程中,定期检查刀具与工件的间隙,根据实际情况进行调整。
对机床进行定期检查,确保其各项性能指标符合要求。
总之,处理数控机床对刀间隙需要综合考虑刀具、机床、加工工艺等多方面因素。通过上述方法,可以有效减少对刀间隙,提高加工精度和加工质量。