如何改善冲压模具热处理变形和开裂现象
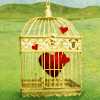
通过优化热处理工艺、选用合适的模具材料和改进模具设计,可以有效改善冲压模具热处理变形和开裂现象。
冲压模具在热处理过程中,由于加热、冷却速度不均,以及热应力和组织转变等因素的影响,容易出现变形和开裂现象。以下是一些改善这些问题的方法:
1. 优化热处理工艺:
控制加热速度:加热速度过快会导致模具内部应力集中,从而引起变形和开裂。应采用适当的加热速度,通常为每小时50-100℃。
严格控制冷却速度:冷却速度对模具组织和性能有重要影响。应避免快速冷却,尤其是在模具的厚大部位,可以通过分级冷却来减少热应力和组织转变引起的变形。
选择合适的热处理温度:不同的模具材料和用途需要不同的热处理温度。应通过实验确定最佳的热处理温度,以确保模具的硬度和韧性达到最佳平衡。
2. 选用合适的模具材料:
根据模具的工作条件和性能要求,选择合适的模具材料。例如,高速钢、模具钢等材料具有较高的热硬性和耐磨性,适合用于高温、高应力工况。
对于易变形和开裂的材料,如灰铸铁,可以通过添加合金元素来提高其性能。
3. 改进模具设计:
减少模具的壁厚差异:厚薄不均的模具在热处理过程中容易产生热应力和变形。设计时应尽量使模具壁厚均匀,减少热处理过程中的应力集中。
采用合理的冷却方式:设计模具时,应考虑冷却通道的布局,确保冷却均匀,减少温差引起的变形。
增加模具的支撑结构:在模具设计时,增加支撑结构可以增强模具的刚性,减少热处理过程中的变形。
4. 采用预拉伸技术:
在模具热处理前,对模具进行预拉伸处理,可以消除模具中存在的残余应力,从而降低热处理过程中的变形和开裂风险。
5. 加强模具的热处理质量控制:
热处理过程中,应严格控制温度、时间、冷却速度等参数,确保模具质量。
定期检测模具的热处理性能,如硬度、韧性等,以确保模具满足使用要求。
通过以上措施,可以有效改善冲压模具热处理变形和开裂现象,提高模具的使用寿命和加工精度。