精益生产之现场改善
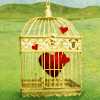
通过现场改善,精益生产能够显著提升效率、减少浪费,并提高产品质量。
精益生产是一种旨在通过最小化浪费和最大化价值来提高生产效率和质量的生产管理方法。现场改善是精益生产的核心环节之一,它涉及对生产现场的全面审视和优化,以下是对现场改善的详细探讨:
1. 识别浪费:现场改善的第一步是识别浪费。浪费包括时间浪费、材料浪费、空间浪费等。通过价值流图(Value Stream Map)等工具,可以直观地看到生产过程中哪些环节是多余的,哪些环节是导致浪费的根源。
2. 5S活动:5S是指整理(Seiri)、整顿(Seiton)、清洁(Seiso)、清扫(Seiketsu)和素养(Shitsuke)。这些活动旨在创造一个有序、清洁、安全的工作环境,减少寻找物品的时间,提高工作效率。
3. 布局优化:优化生产线的布局可以减少运输距离,降低搬运成本,提高生产效率。通过重新规划生产线,可以减少不必要的移动和等待时间。
4. 标准化作业:标准化作业是现场改善的关键。通过制定标准作业程序,可以确保每个操作都能按照既定的最佳方法进行,减少错误和返工。
5. 自动化和改进设备:利用自动化设备可以减少人工操作,提高生产速度和精度。同时,定期维护和改进设备也是减少浪费、提高效率的重要手段。
6. 员工参与:员工的参与是现场改善成功的关键。通过培训和教育,让员工了解精益生产的原则和方法,鼓励他们提出改进建议,可以激发团队的创新精神。
7. 持续改进:现场改善是一个持续的过程,需要不断地审视和改进。通过定期的回顾和评估,可以确保改善措施的有效性,并持续推动生产效率的提升。
具体到现场改善的实践,以下是一些具体的措施:
减少库存:通过实施准时制(JIT)生产,减少原材料和成品的库存,降低仓储成本。
减少不良品:通过质量管理体系,如六西格玛(Six Sigma),减少生产过程中的不良品率。
缩短生产周期:通过优化生产流程,减少每个产品的生产时间,提高响应市场变化的能力。
提高设备利用率:通过预防性维护和优化设备使用,提高设备的运行效率。
总之,现场改善是精益生产的重要组成部分,通过系统地分析和改进生产现场,企业可以实现效率的提升、成本的降低和质量的提高,从而在激烈的市场竞争中占据优势。