数控车床内槽震刀的解决技巧
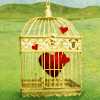
通过调整加工参数、改进刀具设计、优化机床状态以及合理选用切削液等手段,可以有效解决数控车床内槽震刀问题。
数控车床在加工内槽时,常常会遇到震刀的现象,这不仅影响了加工质量,还可能导致刀具损坏和加工效率降低。以下是一些解决数控车床内槽震刀的技巧:
1. 调整加工参数:
切削速度:适当降低切削速度可以减少切削过程中的振动。切削速度应根据材料的性质和刀具的耐用度来确定。
进给量:减小进给量可以减少切削力,从而降低振动的可能性。
切削深度:合理选择切削深度,避免过大的切削深度导致的切削力过大。
2. 改进刀具设计:
刀具形状:优化刀具的形状和几何参数,如前角、后角、主偏角和副偏角,以减少切削过程中的不稳定性。
刀具材料:选择合适的刀具材料,提高刀具的耐磨性和韧性,减少振动的发生。
3. 优化机床状态:
机床精度:确保机床的精度,包括主轴精度、导轨精度和定位精度,以减少加工过程中的误差。
机床调整:定期对机床进行维护和调整,确保机床的各个部件处于最佳工作状态。
4. 合理选用切削液:
切削液类型:根据加工材料选择合适的切削液,如乳化液、油性切削液等,切削液应具有良好的冷却和润滑性能。
切削液流量:适当增加切削液的流量,有助于带走切削过程中的热量,减少振动。
5. 操作技巧:
启动顺序:在启动机床前,先开启切削液,再启动主轴,这样可以减少启动时的振动。
平稳加减速:在加工过程中,应平稳地加减速,避免突然的加速或减速导致的振动。
通过上述措施,可以有效解决数控车床内槽震刀问题,提高加工质量和效率。在实际操作中,应根据具体情况灵活运用这些技巧,以达到最佳的效果。