影响切削性能的因素
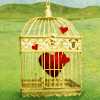
影响切削性能的因素主要包括材料属性、切削工具的几何形状、切削条件、机床性能和切削液。
切削性能是指切削过程中切削工具与工件之间的相互作用以及切削过程中产生的各种物理和化学现象的综合表现。以下是对影响切削性能的几个主要因素的详细分析:
1. 材料属性:工件材料的硬度、韧性、塑性、导热性等都会直接影响切削性能。例如,硬度和塑性的增加会导致切削力的增加,而导热性的降低会使切削过程中产生的热量难以散发,从而影响切削效果。
2. 切削工具的几何形状:切削工具的几何形状包括前角、后角、主偏角、副偏角等。这些角度的变化会影响切削刃的锋利度、切削路径、切削力以及切屑的形成。例如,适当增大前角可以减小切削力,但过大的前角可能导致切削刃的强度下降。
3. 切削条件:切削速度、进给量和切削深度是影响切削性能的关键切削条件。切削速度过快可能导致切削温度过高,工具磨损加剧;进给量过大可能导致切削力过大,工件表面质量下降;切削深度过深则可能导致切削热量集中,影响切削效果。
4. 机床性能:机床的刚性和稳定性对切削性能有显著影响。机床的刚性越好,切削过程中的振动越小,切削精度和表面质量越高。此外,机床的冷却和润滑系统也会影响切削性能。
5. 切削液:切削液在切削过程中起到冷却、润滑和清洗作用。切削液的种类、浓度和使用方式都会影响切削性能。合适的切削液可以降低切削温度,减少刀具磨损,提高切削效率和工件表面质量。
综上所述,影响切削性能的因素是多方面的,需要综合考虑材料属性、切削工具的几何形状、切削条件、机床性能和切削液等因素,以实现高效、高质的切削加工。在实际生产中,应根据具体情况选择合适的切削参数和切削液,以提高切削性能,降低生产成本。