锻件分型面为什么晶粒粗大
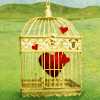
锻件分型面晶粒粗大的原因通常与锻造工艺参数控制不当、材料本身特性以及冷却速度有关。
在锻造过程中,锻件分型面的晶粒粗大是一个常见的问题,它对材料的机械性能和后续加工质量有着重要影响。以下是造成锻件分型面晶粒粗大的几个主要原因:
1. 锻造温度控制不当:锻造温度是影响晶粒尺寸的关键因素。如果锻造温度过高,会导致材料在锻造过程中发生严重的动态再结晶,从而形成粗大的晶粒。相反,如果锻造温度过低,材料可能无法充分变形,导致晶粒长大。
2. 锻造速度和压力不足:在锻造过程中,如果锻造速度和压力不足,材料内部的变形不足以有效破碎原始晶粒,这可能导致晶粒在分型面附近粗大。
3. 冷却速度不均匀:在锻造结束后,锻件的冷却速度对晶粒尺寸有很大影响。如果冷却速度不均匀,局部区域可能会快速冷却,形成细晶,而其他区域则可能因为冷却速度慢而形成粗晶。
4. 材料本身特性:某些材料在高温下具有较高的再结晶倾向,容易在锻造过程中形成粗大晶粒。
5. 锻造工艺参数:如锻造时间、锻造次数等工艺参数设置不当,也可能导致晶粒粗大。
为了减少锻件分型面晶粒粗大的问题,需要严格控制锻造工艺参数,包括适当调整锻造温度、速度、压力和冷却速度等。此外,优化锻造工艺和材料选择也是提高锻件质量的重要措施。通过这些方法,可以有效控制晶粒尺寸,提高锻件的机械性能和加工性能。