高速钢与硬质合金刀具磨损的主要原因
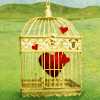
高速钢与硬质合金刀具磨损的主要原因是切削过程中的物理和化学作用,包括高温、高压、摩擦、化学腐蚀以及机械磨损等。
高速钢和硬质合金刀具在金属切削加工过程中,其磨损的主要原因可以从以下几个方面进行详细分析:
1. 物理磨损:切削过程中,刀具与工件接触区域产生极高的压力和温度,导致刀具表面材料在微观尺度上发生塑性变形和磨损。物理磨损主要包括以下几种形式:
磨粒磨损:切削过程中,硬质颗粒如氧化物、硅酸盐等夹在刀具和工件之间,造成刀具表面磨损。
粘着磨损:在高温下,刀具和工件表面发生金属间的粘着,切削后形成粘着层,导致刀具表面磨损。
疲劳磨损:由于切削过程中反复的接触和分离,刀具表面产生微小裂纹,最终扩展导致刀具磨损。
2. 化学磨损:切削过程中,刀具材料与工件材料发生化学反应,导致刀具表面形成脆性化合物,降低了刀具的耐磨性。化学磨损主要包括以下几种形式:
氧化:刀具在高温下与空气中的氧气发生氧化反应,形成氧化层,降低刀具硬度。
溶解:刀具材料与工件材料发生溶解反应,使刀具表面材料流失。
腐蚀:刀具材料在切削过程中与工件材料中的酸、碱等腐蚀性物质发生反应,导致刀具表面腐蚀。
3. 热磨损:切削过程中,刀具表面温度升高,导致刀具材料的热膨胀和软化,从而降低刀具的硬度和强度。热磨损主要表现为以下几种形式:
热裂纹:刀具材料在高温下产生热膨胀,导致内部应力集中,形成裂纹。
热软化:刀具材料在高温下软化,降低刀具的硬度和耐磨性。
4. 机械磨损:切削过程中,刀具表面与工件表面发生剧烈摩擦,导致刀具表面磨损。机械磨损主要包括以下几种形式:
磨损:刀具表面与工件表面发生摩擦,使刀具表面材料逐渐损耗。
崩刃:刀具在切削过程中,由于应力集中或材料性能不足,导致刀具表面产生崩刃。
综上所述,高速钢和硬质合金刀具的磨损是由物理磨损、化学磨损、热磨损和机械磨损等多种因素共同作用的结果。在实际生产中,应根据不同的切削条件和工件材料,选择合适的刀具材料、几何参数和涂层,以降低刀具磨损,提高切削效率和加工质量。