数控车床刀中心不对怎么调整
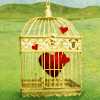
数控车床刀中心不对可以通过以下步骤进行调整:
数控车床刀中心不对是加工过程中常见的问题,如果刀中心偏移,将会导致加工出来的工件尺寸不准确,甚至影响加工质量。以下是一些调整数控车床刀中心的步骤:
1. 检查刀架和刀柄:
首先检查刀架和刀柄是否安装正确,是否有松动或者损坏。如果发现问题,应及时更换或修复。
2. 校准机床坐标系:
确保机床的坐标系正确设置。在数控系统中,坐标系的设置直接影响刀具的位置。如果坐标系设置错误,刀具的实际位置将与编程中的位置不符。
3. 调整刀尖位置:
使用对刀仪或千分尺等测量工具,精确测量刀具的刀尖位置。将测量结果与编程中的刀尖位置进行比较,确定偏差。
4. 调整刀具位置:
根据测量结果,通过以下方法调整刀具位置:
如果刀具向前偏移,可以适当松开刀架的紧固螺丝,然后将刀具向后移动,调整至正确位置后重新紧固。
如果刀具向后偏移,可以适当松开刀架的紧固螺丝,然后将刀具向前移动,调整至正确位置后重新紧固。
5. 调整刀架位置:
如果刀具位置调整后仍然不对,可能需要调整刀架的位置。这通常涉及到调整刀架的导轨或者调整刀架的支撑结构。
6. 使用对刀程序:
在数控系统中,通常有专门的对刀程序,可以帮助用户快速调整刀具位置。运行对刀程序,根据系统提示进行操作。
7. 重复检查和调整:
调整完成后,再次使用测量工具检查刀具位置,确保调整准确。如果仍有偏差,重复上述步骤进行微调。
8. 记录调整数据:
将调整后的刀具位置和机床参数记录下来,以便将来重复加工时使用。
9. 定期检查和维护:
定期检查机床和刀具的磨损情况,及时更换磨损的刀具和磨损严重的机床部件,以保持机床的精度。
通过上述步骤,可以有效地调整数控车床的刀中心,确保加工出的工件尺寸准确。在调整过程中,需要耐心细致,确保每一步操作都符合机床和刀具的技术要求。