内冷钻头冷却孔制造
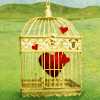
高效的内冷钻头冷却孔制造技术是确保钻头在高温、高压工作条件下性能稳定的关键。
内冷钻头冷却孔的制造是一项精密的技术,它涉及到钻头的冷却效率和耐用性。以下是对内冷钻头冷却孔制造过程的详细阐述:
首先,设计阶段至关重要。设计人员需要根据钻头的具体用途和工作环境,确定冷却孔的形状、大小和分布。冷却孔的形状通常为径向或螺旋状,以最大化冷却液流动面积,提高冷却效果。冷却孔的大小和分布则需确保冷却液能够均匀地到达钻头各个部分,避免局部过热。
制造过程中,首先使用CNC(计算机数控)机床进行粗加工,这一步骤主要去除材料,形成初步的冷却孔形状。随后,进行精加工,这一步骤使用更精细的刀具和更高的精度,以确保冷却孔的尺寸和形状符合设计要求。
为了提高冷却孔的耐磨性和耐腐蚀性,制造过程中常常采用硬质合金或高硬度材料制作刀具。同时,为了确保冷却孔的密封性,加工后需要对冷却孔进行抛光处理,减少孔壁的粗糙度。
在冷却孔制造完成后,还需要进行一系列的测试,包括孔径测量、形状检测和密封性测试,以确保冷却孔能够满足实际工作条件的要求。
此外,随着技术的发展,一些先进的制造技术,如激光加工和电火花加工,也被应用于内冷钻头冷却孔的制造中。这些技术能够实现更高的加工精度和更复杂的孔形设计。
总之,内冷钻头冷却孔的制造是一个涉及材料科学、机械加工和精密测量的复杂过程。通过精确的设计和先进的制造技术,可以确保钻头在极端工作条件下的冷却效率,从而延长钻头使用寿命,提高加工效率。