铝件加工切削液的浓度是多少
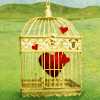
铝件加工切削液的浓度通常在3%到10%之间,具体浓度根据加工工艺和切削液的类型而定。
在铝件加工过程中,切削液的选择和使用对于保证加工质量、延长刀具寿命以及提高生产效率至关重要。切削液的浓度直接影响到其润滑、冷却、防锈和清洗等性能的发挥。
一般来说,铝件加工切削液的浓度范围在3%到10%之间。以下是一些具体的考虑因素和指导原则:
1. 加工工艺:不同的铝件加工工艺对切削液的浓度要求不同。例如,在高速切削或重负荷切削时,切削液的浓度需要较高,通常在8%到10%之间,以确保充分的润滑和冷却。而在低速轻负荷切削时,切削液的浓度可以适当降低,如3%到5%。
2. 切削液的类型:不同的切削液成分和性能会影响其适用浓度。半合成水性切削液,如专为铝合金加工设计的SCC638,通常推荐浓度为5%到10%。这类切削液具有很好的抗氧化保护作用,适合用于各种加工工艺。
3. 环境因素:环境温度和湿度也会影响切削液的浓度选择。在高温或高湿环境下,切削液可能会更快地蒸发,因此可能需要增加浓度以保持其性能。
4. 切削液的原液浓度:切削液原液的浓度通常由制造商提供,用户在使用时需要按照产品说明进行稀释。例如,一些切削液原液的推荐稀释比例为1:20到1:25。
5. 防锈要求:如果加工过程中对防锈有特别要求,切削液的浓度可能需要调整到10%左右,以保证防锈效果。
6. 实际操作:在实际操作中,用户应通过试验和调整来找到最佳的切削液浓度。过高或过低的浓度都可能影响加工效果,如过高可能导致泡沫增多,过低则可能无法有效冷却和润滑。
总之,铝件加工切削液的浓度应根据具体的加工条件、切削液类型和加工要求来确定。正确选择和使用切削液,不仅可以提高铝件加工的质量和效率,还可以延长刀具和设备的寿命,降低生产成本。