影响表面粗糙度的四种因素
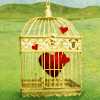
影响表面粗糙度的四种主要因素包括加工方法、刀具选用、工件材料以及磨削条件。
在机械加工过程中,表面粗糙度是衡量加工质量的一个重要指标。表面粗糙度的高低直接影响到零件的耐磨性、密封性、疲劳强度等性能。以下是影响表面粗糙度的四种主要因素:
1. 加工方法:加工方法是影响表面粗糙度的基础因素。不同的加工方法会产生不同的表面粗糙度。例如,车削、磨削、铣削、刨削等加工方法,由于切削方式、切削速度、切削深度等因素的不同,会导致表面粗糙度的差异。一般来说,切削速度越快、切削深度越小,表面粗糙度越低。
2. 刀具选用:刀具的选用对表面粗糙度有直接影响。刀具的锋利程度、几何形状、材料等都会影响表面粗糙度。刀具锋利程度越高,加工过程中产生的塑性变形越小,表面粗糙度越低。刀具的几何形状,如前角、后角、主偏角等,也会影响切削过程中的摩擦和塑性变形,进而影响表面粗糙度。
3. 工件材料:工件材料的性质对表面粗糙度有重要影响。不同材料的切削性能、塑性、硬度等特性不同,导致加工过程中产生的塑性变形和切削力不同,从而影响表面粗糙度。例如,塑性较好的材料在加工过程中容易产生塑性变形,导致表面粗糙度增大。
4. 磨削条件:磨削条件是影响磨削加工表面粗糙度的重要因素。磨削条件包括砂轮的修整、粒度、硬度、磨削速度、磨削径向进给量与光磨次数、下件圆周进给速度与轴向进给量等。例如,砂轮的修整质量越好,表面粗糙度越低;砂轮的粒度越细,表面粗糙度越低;磨削速度越高,表面粗糙度越低。
总之,在机械加工过程中,为了提高零件的表面质量,降低表面粗糙度,需要综合考虑加工方法、刀具选用、工件材料以及磨削条件等因素,采取合理的工艺参数和加工方法,从而提高零件的表面质量。