注塑反压成型过程
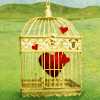
注塑反压成型过程是一种通过在模具腔内施加反向压力来提高塑料制品密实度和表面质量的成型方法。
注塑反压成型过程是一种常见的塑料成型技术,它通过在模具闭合后,对模具腔内尚未凝固的塑料熔体施加一定压力,以达到以下目的:
1. 提高密实度:反压力能够填充熔体中的气泡和孔隙,使制品表面和内部更加密实,提高产品的力学性能和耐腐蚀性。
2. 改善表面质量:反压力有助于减少熔接痕、波纹等表面缺陷,提高制品的外观质量。
3. 减少收缩率:通过反压力,可以减少塑料制品的收缩率,从而减少尺寸公差,提高尺寸精度。
4. 提高生产效率:反压力成型可以缩短冷却时间,加快制品固化速度,提高生产效率。
具体过程如下:
准备阶段:将塑料原料加热熔化,并通过注塑机将熔融塑料注入模具。
反压施加:在模具闭合后,通过注塑机控制系统向模具腔内施加反压力。
成型阶段:在反压力的作用下,熔融塑料在模具腔内均匀分布,并开始凝固。
保压阶段:在熔体固化初期,保持反压力一段时间,以确保制品密实。
脱模:保压完成后,降低反压力,打开模具取出制品。
注塑反压成型技术的应用范围广泛,尤其在汽车、家电、电子等行业中,对于提高塑料制品的质量和性能具有重要意义。