加工表面粗糙度差的原因
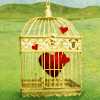
加工表面粗糙度差的主要原因是多方面的,包括加工方法不当、刀具磨损、切削参数选择不当、工件材料特性、机床精度和操作技术等因素。
加工表面粗糙度差是机械加工过程中常见的问题,它直接影响零件的表面质量和使用性能。以下是导致加工表面粗糙度差的一些主要原因:
1. 加工方法不当:不同的加工方法对表面粗糙度有直接的影响。例如,车削、磨削、铣削等加工方法中,切削速度、进给量和切削深度等参数的设置不当,会导致表面粗糙度增大。
2. 刀具磨损:刀具在加工过程中会逐渐磨损,磨损的刀具会导致切削力增大,切削温度升高,从而增加表面粗糙度。因此,定期更换或磨削刀具是必要的。
3. 切削参数选择不当:切削参数如切削速度、进给量和切削深度等对表面粗糙度有显著影响。不合理的切削参数会导致表面塑性变形增加,形成不规则的高低起伏,从而增大粗糙度。
4. 工件材料特性:不同的材料具有不同的加工性能。例如,硬质合金刀具加工钢料时比加工铸铁更容易产生表面粗糙度。
5. 机床精度和稳定性:机床的精度和稳定性对加工表面粗糙度有很大影响。机床精度低或稳定性差会导致工件在加工过程中产生振动,进而影响表面质量。
6. 冷却润滑条件:适当的冷却润滑可以减少切削热,降低工件和刀具的温度,从而减少表面粗糙度。冷却润滑条件不佳会导致切削温度过高,加剧塑性变形,增加粗糙度。
7. 操作技术:操作者的技术水平对加工表面粗糙度也有重要影响。不熟练的操作可能导致切削不均匀,增加表面粗糙度。
为了改善加工表面粗糙度,可以采取以下措施:
优化加工工艺,合理选择切削参数。
定期检查和磨削刀具,确保刀具锋利。
提高机床精度,减少加工过程中的振动。
改善冷却润滑条件,控制切削温度。
提高操作者的技术水平,确保加工过程稳定。
通过上述措施,可以有效减少加工表面粗糙度,提高零件的表面质量。