双相钢热处理后开裂
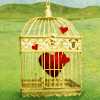
双相钢热处理后开裂的主要原因是热处理过程中的应力集中和冷却速率不当。
双相钢(DP钢)是一种高强度、低韧性的钢种,其通过特殊的成分设计和热处理工艺获得高强度和良好的成形性。然而,在热处理过程中,双相钢可能会出现开裂现象,主要原因包括以下几点:
1. 热应力:在加热过程中,双相钢内部由于不同相的膨胀系数差异,会导致内部应力集中。如果应力超过了材料的屈服极限,就会导致开裂。
2. 冷却速率:冷却速率对双相钢的组织和性能有重要影响。过快的冷却速率会导致马氏体转变,这种转变产生的内应力可能导致开裂。相反,过慢的冷却速率可能无法达到预期的热处理效果,影响钢的性能。
3. 组织转变:双相钢在热处理过程中会发生相变,如果相变不完全或者发生异常,也会导致组织应力,从而引发开裂。
4. 表面质量:表面缺陷如裂纹、划痕等在热处理过程中容易成为应力集中点,增加了开裂的风险。
为了避免双相钢热处理后的开裂,可以采取以下措施:
优化热处理工艺参数,如控制加热温度、保温时间和冷却速率。
使用适当的冷却介质,如油或水,以控制冷却速率。
对材料进行表面处理,去除表面的缺陷。
在热处理前进行预拉伸,以降低应力。
选择合适的合金成分,以改善钢的热处理性能。
通过上述措施,可以有效减少双相钢热处理过程中的开裂风险,提高其最终产品的质量和性能。