通过精益生产管理消除浪费
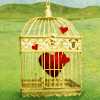
通过精益生产管理,企业可以有效识别和消除生产过程中的浪费,从而提高效率、降低成本,并提升客户满意度。
精益生产管理,起源于日本,是一种旨在通过最小化浪费来提高生产效率和产品质量的管理方法。在实施精益生产的过程中,企业可以从以下几个方面着手消除浪费:
1. 时间浪费的消除:精益生产强调时间的价值,通过缩短生产周期、减少等待时间、减少非增值活动等方式,实现生产流程的优化。
2. 库存浪费的消除:精益生产倡导“即时生产”理念,即只在需要时生产所需数量的产品,以减少库存积压和资金占用。
3. 流程浪费的消除:通过分析生产流程,识别并消除不必要的步骤和环节,简化操作流程,提高工作效率。
4. 运动浪费的消除:在生产线布局和操作中,减少不必要的移动和搬运,优化生产线布局,提高操作便利性。
5. 缺陷浪费的消除:通过质量控制和持续改进,减少产品缺陷,降低返工和维修成本。
具体实施步骤如下:
价值流分析:首先,企业需要对生产流程进行价值流分析,识别出价值流中的各个环节,以及其中的浪费。
5S活动:通过整理(Seiri)、整顿(Seiton)、清扫(Seiso)、清洁(Seiketsu)、素养(Shitsuke)这五个步骤,改善工作环境,减少浪费。
看板系统:实施看板系统,通过可视化管理,实时监控生产进度,避免过量生产和等待。
持续改进:通过PDCA(计划-执行-检查-行动)循环,不断优化生产流程,提高生产效率。
通过实施精益生产管理,企业可以实现以下效益:
提高生产效率:通过消除浪费,减少非增值活动,提高生产效率。
降低成本:减少库存、减少缺陷、降低能源消耗等,从而降低生产成本。
提升产品质量:通过持续改进,提高产品质量,满足客户需求。
增强企业竞争力:提高生产效率、降低成本、提升产品质量,使企业在激烈的市场竞争中占据有利地位。
总之,通过精益生产管理消除浪费,是企业提高生产效率和产品质量、实现可持续发展的重要途径。