注塑成型中缩水改善
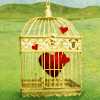
通过优化注塑成型工艺参数和材料选择,可以有效改善注塑成型中的缩水问题。
注塑成型是一种广泛应用于塑料制品生产的工艺,然而在这个过程中,缩水问题常常是困扰生产者的难题。缩水是指塑料在冷却固化过程中由于收缩率不一致而导致的尺寸精度降低,影响产品质量。以下是一些改善注塑成型中缩水问题的方法:
1. 材料选择:选用适当的塑料材料是减少缩水的基础。不同塑料的收缩率不同,选择收缩率较低的材料可以减少缩水现象。
2. 成型温度控制:合理设置模具温度和熔体温度。模具温度应适中,过高或过低都会导致塑料收缩率增大。熔体温度则应控制在材料的最适温度范围内,以确保熔体流动性好,减少冷却速度不均。
3. 模具设计:优化模具设计,减少浇口和冷却通道的长度差异,避免冷却不均。合理设计冷却系统,确保模具内各部分的冷却均匀。
4. 注塑参数调整:调整注塑压力、速度和保压压力等参数,以控制熔体在模具内的流动和冷却速度。适当的注塑参数可以使塑料均匀填充模具,减少缩水。
5. 热处理:对塑料制品进行热处理,如退火、时效处理等,可以改善塑料的结晶度,提高其尺寸稳定性。
6. 模具保养:定期对模具进行保养和维护,确保模具表面光滑,减少摩擦和热量损失,从而降低塑料的收缩率。
7. 生产过程监控:在生产过程中,实时监控注塑成型参数和产品尺寸,及时调整工艺参数,确保产品质量。
通过上述方法,可以有效改善注塑成型中的缩水问题,提高塑料制品的尺寸精度和外观质量。