橡胶硫化不好什么原因
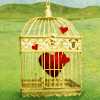
橡胶硫化不好可能由多种原因引起,包括原料问题、设备故障、工艺参数不当、环境因素等。
橡胶硫化是橡胶制品生产过程中的关键步骤,它通过化学反应使橡胶材料从生胶转变为具有弹性和强度的硫化胶。然而,在硫化过程中,可能会出现硫化不良的情况,影响橡胶产品的质量和性能。以下是一些可能导致橡胶硫化不良的原因:
1. 原料问题:
生胶质量问题:生胶中可能含有杂质或未反应完全的原料,导致硫化不均匀。
配合剂问题:如促进剂、抗氧化剂等配合剂添加不当或质量不佳,会影响硫化速度和硫化程度。
2. 设备故障:
硫化模具问题:模具设计不合理或磨损严重,可能导致硫化不均匀。
硫化设备故障:如温度控制不准确、压力不足等,都会影响硫化效果。
3. 工艺参数不当:
温度控制:硫化温度过高或过低都会影响硫化效果。温度过高可能导致橡胶过早老化,过低则硫化不完全。
硫化时间:硫化时间过短或过长都会影响硫化效果。时间过短可能导致硫化不完全,时间过长则可能导致橡胶过度交联,失去弹性。
压力:硫化压力不足可能导致硫化不均匀,压力过高则可能损坏橡胶。
4. 环境因素:
湿度:湿度过高可能导致硫化不完全,因为水分会与橡胶中的某些成分发生反应,影响硫化效果。
温度波动:环境温度波动过大也可能导致硫化过程不稳定。
5. 操作不当:
混合不均匀:橡胶与配合剂混合不均匀可能导致硫化不均匀。
装模不当:装模过程中如果出现气泡或杂质,可能会影响硫化效果。
为了确保橡胶硫化质量,生产过程中需要对原料、设备、工艺参数和环境进行严格控制和监控,及时发现并解决问题。