如何合理选择铣削用量
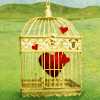
合理选择铣削用量应综合考虑工件材料、铣刀材料、机床性能、加工精度要求等因素,以达到最佳加工效果和经济效益。
在机械加工中,铣削是一种常见的加工方法,其铣削用量包括铣削速度、进给量和切削深度。合理选择铣削用量对于保证加工质量、提高生产效率以及降低成本具有重要意义。以下是如何合理选择铣削用量的几点建议:
1. 工件材料:不同材料的工件具有不同的切削性能。例如,钢料比铸铁和铝材更难切削,因此需要更高的铣削速度和切削深度。在确定铣削用量时,首先要了解工件材料的性质,如硬度、韧性等。
2. 铣刀材料:铣刀的材料也会影响铣削用量。高速钢铣刀适用于中等硬度的材料,而硬质合金铣刀适用于硬度较高的材料。选择合适的铣刀材料可以确保铣削过程的顺利进行。
3. 机床性能:机床的功率、刚性、精度等因素都会影响铣削用量。在选择铣削用量时,要确保机床的性能能够满足加工要求,避免因机床不足而影响加工质量。
4. 加工精度要求:加工精度是选择铣削用量的重要依据。对于高精度要求的工件,应适当降低铣削速度和进给量,以减小切削力,避免工件变形。
5. 铣削速度:铣削速度是指铣刀每分钟旋转的圈数。合适的铣削速度可以保证切削热及时散出,避免工件和铣刀过热。一般来说,高速钢铣刀的铣削速度范围为50-200m/min,硬质合金铣刀的铣削速度范围为300-600m/min。
6. 进给量:进给量是指铣刀每转一圈沿工件移动的距离。进给量过大可能导致工件表面粗糙度增加,进给量过小则影响加工效率。进给量应根据铣刀直径、工件材料、机床性能等因素综合考虑。
7. 切削深度:切削深度是指铣刀在工件上切削的深度。切削深度过大可能导致工件变形、铣刀磨损加剧,切削深度过小则影响加工效率。切削深度应根据工件材料、铣刀材料、机床性能等因素确定。
总之,合理选择铣削用量需要综合考虑多种因素。在实际操作中,可以通过试验和经验不断优化铣削用量,以达到最佳加工效果和经济效益。