废机油淬火和水淬火不同
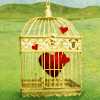
废机油淬火和水淬火在冷却速度、表面硬度、热处理效果和环境影响等方面存在显著差异。
废机油淬火和水淬火是两种常见的金属热处理工艺,它们在冷却介质的选择上有所不同,这直接影响了热处理的效果和过程。
首先,废机油淬火使用的是废机油作为冷却介质。废机油具有较好的导热性和润滑性,能够快速带走工件表面的热量,使工件迅速冷却。这种冷却方式的特点是冷却速度相对较慢,适合于一些对硬度和韧性要求较高的工件。在废机油淬火过程中,工件表面会形成一层油膜,这有助于提高工件表面的光洁度和耐磨性。然而,废机油淬火也存在一些缺点,如油膜难以去除,可能会影响工件的后续加工和使用。
相比之下,水淬火使用的是水作为冷却介质。水具有极高的冷却能力,能够迅速降低工件温度,使得工件表面硬度迅速提高。水淬火适用于要求表面硬度较高的工件,如高速钢刀具和模具等。水淬火的优点是冷却速度快,工件表面硬度高,且成本较低。但是,水淬火也存在一些缺点,如冷却速度过快可能导致工件内部应力集中,容易引发裂纹;此外,水淬火对工件表面的光洁度影响较大,可能会出现氧化和腐蚀现象。
在热处理效果方面,废机油淬火和水淬火也有明显的区别。废机油淬火由于冷却速度较慢,工件内部应力较小,因此工件的热处理变形和开裂风险较低。而水淬火由于冷却速度过快,容易导致工件内部应力增大,从而增加工件变形和开裂的风险。
最后,从环境影响角度来看,废机油淬火存在一定的环境污染问题。由于废机油中可能含有有害物质,如果不经过处理直接排放,会对环境造成污染。而水淬火则相对环保,因为水是一种可再生的资源,不会对环境造成污染。
综上所述,废机油淬火和水淬火在冷却速度、表面硬度、热处理效果和环境影响等方面存在显著差异。在实际应用中,应根据工件的材料、性能要求以及成本等因素综合考虑,选择合适的淬火工艺。