精益生产的常用工具
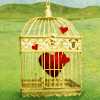
精益生产的常用工具主要包括价值流图、5S管理、看板系统、持续改进的PDCA循环、快速换模技术、防错技术等。
精益生产,作为一种以最小化浪费和最大化价值创造为核心理念的生产管理方式,其成功实施依赖于一系列实用且高效的工具。以下是一些精益生产的常用工具:
1. 价值流图(Value Stream Mapping,VSM):这是一种描绘产品从原材料到成品整个生产过程的工具。通过绘制价值流图,企业可以清晰地识别出生产过程中的浪费点,从而进行改进。
2. 5S管理:5S分别是整理(Seiri)、整顿(Seiton)、清扫(Seiso)、清洁(Seiketsu)和素养(Shitsuke)。5S管理通过规范现场环境,提高员工素质,达到减少浪费、提高工作效率的目的。
3. 看板系统(Kanban):看板是一种视觉管理工具,通过卡片或信号来控制生产流程。看板系统有助于实现准时生产(JIT),减少库存积压,提高生产效率。
4. 持续改进的PDCA循环:PDCA循环包括计划(Plan)、执行(Do)、检查(Check)和处理(Act)四个阶段。通过不断循环PDCA,企业可以不断改进生产过程,提高产品质量。
5. 快速换模技术(SMED):快速换模技术旨在缩短产品更换模具的时间,降低换模成本。通过优化操作步骤、减少工具和设备的更换次数,实现快速换模。
6. 防错技术(Poka-Yoke):防错技术是一种通过设计产品或生产流程来防止错误的产生。通过在设计和制造过程中加入防错机制,可以减少生产过程中的错误和浪费。
7. 全面质量管理(TQM):TQM强调全员参与,通过持续改进和全员参与,提高产品质量和客户满意度。
8. 看板系统(Kanban):看板系统通过卡片或信号来控制生产流程,实现准时生产(JIT),减少库存积压,提高生产效率。
9. 全员参与改善(TPM):TPM强调全员参与,通过提高员工技能和素质,实现设备维护和生产效率的提升。
这些精益生产的常用工具,有助于企业在生产过程中识别浪费、提高效率、降低成本,从而实现持续改进和提升竞争力。