注塑件变形由哪些因素造成的
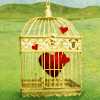
注塑件变形主要由材料特性、模具设计、加工工艺、环境因素以及操作不当等多种因素造成的。
注塑件变形是注塑加工中常见的问题,它不仅影响了产品的外观,还可能影响产品的性能和使用寿命。以下是导致注塑件变形的一些主要因素:
1. 材料特性:不同的塑料材料具有不同的热膨胀系数和收缩率。如果选用的塑料材料不适合注塑件的设计要求,如收缩率不匹配,就可能导致变形。
2. 模具设计:
冷却系统:冷却不均匀会导致材料收缩不一致,从而引起变形。
浇口和流道设计:不合理的浇口和流道设计可能导致熔体流动不均匀,造成应力集中和变形。
模具结构:模具的刚性、强度和稳定性不足也可能导致在注塑过程中产生变形。
3. 加工工艺:
注射压力和速度:过高的注射压力和速度可能导致材料在模具内部流动不均,形成内部应力。
保压压力和时间:保压压力和时间不当也会影响材料的收缩均匀性,从而导致变形。
脱模温度:脱模温度过低或过高都会影响注塑件的尺寸稳定性和表面质量。
4. 环境因素:
温度和湿度:生产环境的温度和湿度变化可能会影响塑料的物理性能,进而导致变形。
运输和存储条件:不当的运输和存储条件,如温差过大或受到冲击,也可能引起注塑件变形。
5. 操作不当:
机器调试:机器的调试不当,如压力和温度设置不准确,也可能导致注塑件变形。
操作人员:操作人员的经验不足或操作不规范,如过早脱模或注射压力不足,也会引起变形。
为了减少注塑件变形,需要综合考虑上述因素,并在设计、材料选择、工艺参数设定和生产管理等方面进行优化。