精益生产如何改善工厂
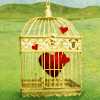
精益生产通过消除浪费、提高效率和质量,显著改善工厂的运作。
精益生产(Lean Manufacturing)是一种以最小化浪费和最大化价值创造为核心的生产管理哲学。它起源于日本,由丰田汽车公司发展而来,现已成为全球制造业追求的目标之一。以下是如何通过精益生产改善工厂的几个关键方面:
1. 消除浪费:
时间浪费:通过缩短生产周期,减少在制品库存,优化生产流程,精益生产可以显著减少生产时间浪费。
资源浪费:精益生产强调资源的有效利用,包括人力、材料、设备等,通过合理规划和优化配置,减少资源浪费。
库存浪费:通过实施看板管理(Kanban)等工具,实现实时库存管理,避免过量库存带来的成本增加。
2. 提高效率:
简化流程:精益生产通过持续改进(Kaizen)的原则,不断优化生产流程,去除不必要的步骤,提高整体效率。
标准化作业:通过标准化作业方法,如5S(整理、整顿、清扫、清洁、素养),提高工作效率,减少错误和返工。
自动化:合理运用自动化设备和技术,减少人力依赖,提高生产速度和精度。
3. 提升质量:
预防胜于检查:精益生产注重在产品生产过程中预防缺陷,而非事后检查,从而提高产品质量。
全面质量管理(TQM):通过全员参与质量管理,从设计到生产再到服务,确保每个环节的质量。
4. 增强灵活性:
多技能员工:通过培训员工掌握多种技能,提高工厂应对市场变化的能力。
柔性生产线:通过模块化设计生产线,使工厂能够快速适应产品更换和生产量变化。
5. 持续改进:
持续改进文化:在工厂中建立持续改进的文化,鼓励员工不断提出改进建议,实现生产流程的不断优化。
通过实施精益生产,工厂可以实现以下具体改善:
成本降低:减少浪费意味着降低成本,提高利润率。
交货期缩短:更高效的流程和库存管理使得产品能够更快地交付给客户。
客户满意度提升:高质量的产品和快速的服务能够提高客户满意度。
员工参与度提高:精益生产鼓励员工参与改进,提高员工的满意度和忠诚度。
总之,精益生产不仅是一种管理工具,更是一种全面的管理哲学,它通过系统化的方法,全面改善工厂的运作,提升企业的竞争力。