如何确定各工序加工尺寸
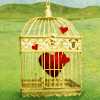
通过综合考虑毛坯尺寸、零件设计尺寸、加工误差、材料特性、加工方法等因素,逐步确定各工序的加工尺寸。
在机械制造过程中,确定各工序的加工尺寸是确保产品质量和加工效率的关键步骤。以下是一些确定各工序加工尺寸的基本原则和方法:
1. 毛坯尺寸的确定:
毛坯尺寸是加工的第一步,其尺寸需大于零件设计尺寸,以便在后续的加工过程中去除多余的金属。
毛坯尺寸的确定应考虑材料性质、铸造或锻造的工艺参数、毛坯的加工余量等因素。
2. 零件设计尺寸的确定:
零件设计尺寸直接来源于工程图纸,是加工尺寸的基础。
设计尺寸应满足零件的功能要求和使用条件,同时考虑加工公差和表面质量。
3. 加工余量的计算:
加工余量是指从毛坯到零件最终尺寸之间需要去除的金属量。
加工余量分为总余量和工序余量。总余量是毛坯尺寸与零件设计尺寸之差,工序余量则是后续每道工序需去除的金属量。
计算加工余量时,需要考虑上工序的加工误差和本工序的加工要求。
4. 工序尺寸的确定:
工序尺寸是指每道工序完成后零件的尺寸。
工序尺寸的确定应基于上工序的尺寸和本工序的加工余量。
为了保证零件的精度和表面质量,工序尺寸应留有适当的公差。
5. 加工误差和公差的分配:
在确定工序尺寸时,需要合理分配加工误差和公差。
加工误差通常包括定位误差、形状误差和尺寸误差等。
公差分配要考虑各工序的加工能力、设备精度和零件的功能要求。
6. 加工方法的选用:
根据零件的材料、形状、尺寸和加工精度要求,选择合适的加工方法。
加工方法的选择将直接影响工序尺寸的确定和加工质量。
7. 实际加工条件的考虑:
在确定工序尺寸时,还需考虑实际加工条件,如机床的加工能力、刀具的磨损等。
总之,确定各工序加工尺寸是一个综合性的过程,需要结合多种因素进行考虑和计算。通过上述步骤,可以确保零件加工的精度、表面质量和加工效率。