挤压模具工作带余量大
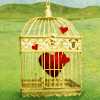
挤压模具工作带余量大,指的是在工作带上预留出一定的材料厚度,以便在挤压过程中,材料能够顺利通过模具并形成所需的型材形状。
挤压模具工作带余量大是铝型材挤压过程中一个非常重要的设计参数。在工作带设计中,余量的大小直接影响到挤压产品的质量、模具的使用寿命以及生产效率。以下将详细阐述挤压模具工作带余量大的原因和重要性。
首先,挤压模具工作带余量大有助于保证型材的尺寸精度。在挤压过程中,金属在受到外力作用下会产生变形,而工作带余量可以提供一定的空间,使得金属在变形后仍能保持所需的尺寸精度。如果工作带余量过小,则可能导致型材尺寸超差,影响产品的使用性能。
其次,挤压模具工作带余量大有利于降低挤压力。在工作带设计中,合理的余量可以使金属在挤压过程中形成平滑的过渡,减少摩擦阻力,降低挤压力。这不仅有利于提高生产效率,还可以延长模具的使用寿命。
此外,挤压模具工作带余量大有助于提高型材的表面质量。在工作带上设置一定的余量,可以使金属在挤压过程中形成均匀的流动,减少焊合线、夹杂等缺陷的产生,提高型材的表面质量。
然而,挤压模具工作带余量大也存在一定的弊端。首先,过大的工作带余量会增加原材料消耗,提高生产成本。其次,在工作带设计中,余量过大可能导致型材截面形状发生改变,影响产品的使用性能。
为了解决这一问题,设计师需要根据实际情况,综合考虑以下因素:
1. 挤压材料:不同材料的挤压性能不同,工作带余量的大小应有所不同。
2. 型材截面形状:不同截面形状的型材,工作带余量的大小也应有所区别。
3. 挤压设备:不同挤压设备的挤压能力不同,工作带余量的大小应与之相适应。
4. 生产效率:在保证产品性能的前提下,适当减小工作带余量,以提高生产效率。
总之,挤压模具工作带余量大是铝型材挤压过程中的一个关键参数。合理的设计工作带余量,可以保证型材的质量、降低生产成本、提高生产效率。设计师在实际工作中,应根据具体情况进行综合分析,以达到最佳的设计效果。