吹塑模头一边厚一边薄怎么调
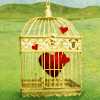
通过调整吹塑模头的流道设计、模具温度、压力控制以及冷却系统来实现模头一边厚一边薄的问题。
在吹塑成型过程中,模头一边厚一边薄的现象称为“厚度不均”,这会影响产品的质量和外观。以下是一些调整方法:
1. 流道设计调整:
流道长度:增加较厚一侧的流道长度,可以使熔体在该侧有更充分的时间流动和冷却,从而增加该侧的厚度。
流道截面:调整流道截面,使较厚一侧的流道截面较大,有利于熔体在该侧形成较厚的壁厚。
分流器:使用分流器来调整熔体的流动方向,使得熔体在进入模具时能够均匀分布,减少厚度不均。
2. 模具温度控制:
模具温度:提高模具较薄一侧的温度,可以加快该侧的冷却速度,从而增加厚度。
温度梯度:在模具上设置温度梯度,使得较厚一侧的温度低于较薄一侧,有助于熔体在较厚一侧形成较厚的壁厚。
3. 压力控制:
压力分布:调整吹塑压力,使得熔体在模具内均匀分布,减少厚度不均。
压力时间:控制压力施加的时间,使得熔体在模具内有足够的时间填充,特别是在较薄一侧。
4. 冷却系统调整:
冷却水路:优化冷却水路设计,确保冷却水能够均匀地分布在模具的各个部分,特别是较薄一侧。
冷却水流量:调整冷却水流量,使得模具在较薄一侧能够快速冷却,从而增加该侧的厚度。
5. 其他因素:
原材料:选择合适的原材料,不同的原材料在冷却速度和收缩率上有所不同,可能影响厚度分布。
工艺参数:优化其他工艺参数,如模具开启速度、吹塑速度等,以减少厚度不均。
通过上述方法,可以在一定程度上调整吹塑模头一边厚一边薄的问题。在实际操作中,可能需要多次试验和调整,以达到最佳的生产效果。同时,生产过程中的监控和数据分析也非常重要,可以帮助及时发现并解决厚度不均的问题。