数控车床内孔粗糙度差怎么解决
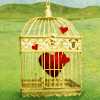
数控车床内孔粗糙度差可以通过优化刀具选择、调整切削参数、改善机床状态和加强加工过程控制等多种方法来解决。
数控车床内孔加工粗糙度差是影响工件表面质量的重要因素,以下是一些解决这一问题的方法:
1. 优化刀具选择:
选择合适的刀具材料,如高速钢、硬质合金等,根据加工材料和加工要求进行选择。
使用精加工刀具,如超细颗粒金刚石(PCD)或立方氮化硼(CBN)刀具,以提高加工表面的光洁度。
确保刀具的几何形状、刀尖半径和切削角度与加工要求相匹配。
2. 调整切削参数:
降低切削速度,以减少切削热和刀具磨损,提高表面光洁度。
适当增加进给量,但避免过大导致表面粗糙度增加。
选择合适的冷却液,并确保冷却效果良好,减少切削温度对表面粗糙度的影响。
3. 改善机床状态:
定期检查和保养机床,确保导轨、主轴等关键部件的精度和润滑状态良好。
检查刀具安装是否牢固,避免因刀具松动导致的表面粗糙度增加。
调整机床的转速和进给,使加工过程稳定,减少振动。
4. 加强加工过程控制:
在加工前对工件进行预加工,如粗加工,以减少后续精加工的切削量,从而降低表面粗糙度。
实施在线检测,实时监控加工过程中的各项参数,一旦发现异常立即调整。
对操作人员进行培训,提高其操作技能和加工意识。
5. 其他方法:
采用多刃刀具进行加工,以实现更高的表面光洁度。
使用超声波辅助加工技术,通过超声波振动减少加工过程中的振动和切削力,提高表面质量。
在加工过程中使用切削液,以减少刀具磨损和热影响,提高加工精度。
总之,解决数控车床内孔粗糙度差的问题需要综合考虑刀具、切削参数、机床状态和加工过程等多个方面,通过优化和调整,实现高质量的内孔加工。