塑料成型的工艺特点有哪些
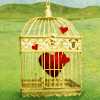
塑料成型的工艺特点主要包括物料的塑化处理、精确的温度和压力控制、以及高效的生产流程。
塑料成型是一种广泛应用于工业生产中的技术,它通过加热和压力将塑料原料塑造成所需的形状和尺寸。以下是一些塑料成型工艺的主要特点:
1. 物料的塑化处理:在塑料成型过程中,首先需要对聚合物进行塑化处理。这一步骤涉及将聚合物加热至熔融状态,以便于后续的成型操作。塑化过程中,聚合物在加热和剪切力的作用下,分子链会发生取向和排列,从而提高材料的流动性和强度。塑化处理通常在双辊炼塑机或密炼机中进行,通过控制温度和时间来确保物料充分塑化。
2. 精确的温度控制:温度是塑料成型工艺中一个至关重要的参数。不同的塑料材料对温度的敏感度不同,因此需要根据具体材料特性来设定合适的温度。例如,料筒温度需要保证物料能够顺利塑化,但又不能过高以免引起分解。喷嘴温度通常略低于料筒最高温度,以防止熔料在喷嘴处发生流延现象。模具温度则影响塑料的流动和冷却速度,进而影响最终产品的尺寸精度和表面质量。
3. 压力控制:在注射成型等塑料成型工艺中,压力是推动熔融塑料流动并填充模具型腔的关键因素。压力的大小需要根据塑料的种类、模具的复杂程度和产品的尺寸要求来精确控制。适当的压力有助于提高成型效率和产品质量。
4. 高效的生产流程:塑料成型工艺通常采用自动化生产线,从原料准备、塑化、注射、冷却到脱模等环节都实现了自动化,大大提高了生产效率。自动化生产线不仅可以减少人工成本,还能确保产品质量的一致性。
5. 物料混合均匀性:为了确保成型产品内部结构的均匀性,塑料成型工艺中需要对物料进行初步混合。这一过程在聚合物熔点温度以下进行,以较小的剪切力促进物料的均匀分布。
6. 环保和健康考虑:随着环保意识的提高,塑料成型工艺越来越注重使用对人体和环境无害的添加剂。在生产过程中,也会采取各种措施减少能耗和排放,以实现可持续发展。
总之,塑料成型工艺具有物料塑化处理、精确的温度和压力控制、高效的生产流程、物料混合均匀性以及环保健康等特点,这些特点共同保证了塑料成型产品的质量和生产效率。