模具损坏的原因及解决方法
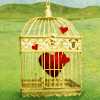
模具损坏是注塑行业常见的质量问题,了解其原因并采取相应措施可以有效预防和解决。
模具损坏是注塑生产过程中不可避免的问题,它不仅影响生产效率,还会增加成本。以下是模具损坏的一些常见原因及相应的解决方法:
1. 材料选择不当:
原因:使用不适合注塑材料的模具,如硬度过高或过低。
解决方法:选择合适的模具材料,如采用高硬度、耐磨损的合金钢。
2. 模具设计缺陷:
原因:模具设计不合理,如冷却水道设计不当、模具厚度不均匀等。
解决方法:优化模具设计,确保冷却均匀,提高模具的强度和耐久性。
3. 加工质量问题:
原因:模具加工精度不够,表面粗糙度过高,导致材料磨损加剧。
解决方法:提高模具加工精度,确保表面光滑,减少材料磨损。
4. 操作不当:
原因:操作人员对模具使用不当,如温度控制不稳定、压力过高或过低。
解决方法:加强操作人员培训,严格按照操作规程进行生产,确保工艺参数的稳定。
5. 模具维护保养不足:
原因:模具在使用过程中未得到及时清洗和保养,导致模具内部积碳、锈蚀。
解决方法:定期对模具进行清洗和保养,使用专门的模具清洗剂,避免锈蚀和积碳。
6. 注塑工艺参数不合理:
原因:注塑温度、压力、速度等参数设置不当,导致模具过热或应力集中。
解决方法:根据材料特性和产品要求,调整注塑工艺参数,确保模具在合适的温度和压力下工作。
7. 模具磨损:
原因:模具长时间使用,表面磨损严重。
解决方法:定期更换模具或对模具进行表面修复,如电火花加工、喷丸处理等。
总之,预防模具损坏需要从材料选择、模具设计、加工质量、操作规范、维护保养和工艺参数调整等多个方面入手。通过这些措施,可以有效延长模具的使用寿命,提高注塑产品的质量。