铸钢冷裂纹产生的原因
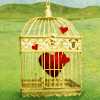
铸钢冷裂纹产生的原因主要与焊接材料、焊接工艺、材料本身的性能以及冷却条件等因素有关。
铸钢冷裂纹的产生通常与以下几个原因密切相关:
1. 焊接材料因素:焊接材料中若含有较高比例的硫、磷等有害元素,这些元素在焊接过程中容易形成低熔点共晶体,导致焊接接头的韧性降低,从而容易产生冷裂纹。
2. 焊接工艺因素:
焊前预热不足:铸钢焊接前若未进行适当的预热,会导致材料冷却速度过快,增加冷裂纹的风险。
焊接速度过快:焊接速度过快会导致热影响区较大,容易形成硬脆的马氏体组织,从而降低接头的韧性。
层间温度控制不当:层间温度过高或过低都会影响焊接接头的性能,增加冷裂纹的产生。
3. 材料本身的性能:
材料化学成分:某些铸钢成分如碳、锰、硅等含量较高时,其淬硬倾向增大,容易产生冷裂纹。
焊接接头的组织状态:焊接接头若形成过多的淬硬组织,如马氏体等,会降低其韧性。
4. 冷却条件:
冷却速度:焊接接头的冷却速度过快,容易导致局部区域产生较大的拉应力,从而产生冷裂纹。
环境湿度:焊接环境湿度较大时,焊接接头表面容易吸附水分,水分在焊接过程中释放氢气,氢气在冷却过程中容易导致冷裂纹。
为预防和减少铸钢冷裂纹的产生,应采取相应的措施,如优化焊接材料、控制焊接工艺参数、加强焊前预热和层间温度控制等。