挤压模具怎么生产的
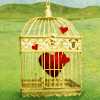
挤压模具的生产是一个复杂而精细的过程,它涉及以下主要步骤:
1. 设计阶段:
需求分析:根据产品要求,确定挤压模具的规格、尺寸、材料要求等。
结构设计:使用专业软件进行三维建模,设计模具的内部结构,包括挤压腔、导向系统、冷却系统等。
优化设计:对模具设计进行优化,确保其强度、刚度和耐磨性,同时考虑生产效率。
2. 材料选择:
根据模具的使用环境和材料特性选择合适的模具钢,如Cr12MoV、H13等。
考虑模具的工作温度、硬度、韧性等性能要求。
3. 加工制造:
毛坯准备:根据模具图纸,加工模具的毛坯,通常是通过铸造或锻造获得。
粗加工:使用车床、铣床等设备进行粗加工,初步形成模具的轮廓。
精加工:使用数控机床进行精加工,确保模具的尺寸精度和表面光洁度。
热处理:对模具进行退火、调质、淬火等热处理,以提高模具的硬度和耐磨性。
4. 装配与调试:
将模具的各个部分装配在一起,进行试装,确保各部件之间的配合精度。
调试模具,调整模具的位置和间隙,保证挤压过程中的稳定性和产品的质量。
5. 检验与试验:
尺寸检验:使用测量工具对模具的尺寸进行精确测量,确保符合设计要求。
性能试验:进行挤压试验,检验模具的耐磨性、强度和耐用性。
表面质量检查:检查模具表面的光洁度和无裂纹等缺陷。
6. 交付与售后:
将合格的模具交付给客户,并提供必要的技术支持和售后服务。
整个挤压模具的生产过程需要专业的技术知识和丰富的实践经验。设计师、工程师和操作人员需要紧密合作,确保模具的质量和效率。随着技术的进步,计算机辅助设计(CAD)和计算机辅助制造(CAM)等先进技术的应用,使得挤压模具的生产更加高效和精确。