注塑模具滑块装配间隙是多少
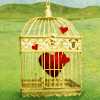
注塑模具滑块装配间隙通常在0.02mm到0.05mm之间,具体数值需根据模具的设计要求和产品精度来确定。
注塑模具滑块装配间隙是注塑模具设计中的一个重要参数,它直接影响到注塑产品的质量和模具的使用寿命。滑块装配间隙指的是滑块与模具型腔之间的间隙,这个间隙过大或过小都会对注塑过程产生不良影响。
首先,我们来了解一下为什么需要设置滑块装配间隙。在注塑过程中,塑料熔体在高温高压下注入模具型腔,随着冷却固化,塑料逐渐变硬。当塑料达到一定硬度时,模具开始开模,此时滑块需要带动型芯移动,以便取出注塑产品。滑块与型腔之间的间隙是为了在开模时能够顺利取出产品,同时避免产品在取出过程中受到损坏。
以下是影响滑块装配间隙的几个因素:
1. 产品精度要求:如果产品精度要求较高,那么滑块装配间隙应相应减小,以保证产品尺寸的准确性。
2. 模具材料:不同材料的模具,其膨胀系数不同,因此滑块装配间隙也会有所不同。
3. 注塑材料:不同塑料的收缩率不同,也会影响滑块装配间隙的设定。
4. 模具结构:模具的结构设计,如滑块与型芯的配合方式,也会影响间隙的设置。
一般来说,注塑模具滑块装配间隙的设定范围如下:
对于要求较高的精密注塑产品,间隙可以设定在0.02mm到0.03mm之间。
对于一般注塑产品,间隙可以设定在0.03mm到0.05mm之间。
如果间隙过小,可能会导致以下问题:
滑块与型芯配合过紧,影响模具的开启和闭合动作,增加能耗。
产品取出困难,容易造成产品变形或损坏。
模具磨损加剧,缩短模具使用寿命。
如果间隙过大,可能会导致以下问题:
产品尺寸精度下降,影响产品性能。
产品表面质量差,出现气泡、划痕等缺陷。
模具开模时产品掉落,影响生产效率。
因此,在设计和制造注塑模具时,需要根据具体的产品要求、模具材料和注塑材料等因素,合理设定滑块装配间隙,以保证注塑产品的质量和模具的长期稳定运行。