如何选用合适的切削液呢
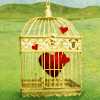
选用合适的切削液需要综合考虑工件材料、加工方法、机床要求以及切削液的性能等因素。
在机械加工过程中,切削液的作用不容忽视,它能够有效降低切削温度、减小切削力、减少刀具磨损、提高加工效率和工件表面质量。以下是一些选用切削液的要点:
1. 工件材料:根据工件材料的不同,切削液的选择也有所区别。例如,切削塑性材料(如钢、铸铁等)时,切削液能有效降低切削温度,减少刀具磨损;而对于脆性材料(如铸铁、青铜等),切削液的冷却效果可能不如润滑效果重要。
2. 加工方法:加工方法的不同决定了切削液的需求。对于粗加工,如车削、铣削等,切削液主要起冷却作用,可选用水基切削液或低浓度乳化液;而对于精加工,如拉削、攻丝等,切削液需要具备良好的润滑性能,可选择极压切削油或高浓度乳化液。
3. 机床要求:不同机床对切削液的要求不同,应根据机床说明书规定的切削液品种进行选择。若没有特殊要求,不要轻易更改切削液品种,以免影响机床性能或造成损坏。
4. 切削液性能:切削液性能是选用切削液的关键。常见的切削液有水溶液、乳化液、矿物油、极压切削油等。水溶液冷却效果最好,但润滑效果较差;极压切削油润滑效果最好,但成本较高。根据实际需求,选择合适的切削液。
5. 切削液添加剂:切削液添加剂可提高切削液的性能,如极压添加剂、防锈剂、抗泡剂等。根据加工需求,添加适量的添加剂,以充分发挥切削液的作用。
6. 安全与环保:选用切削液时,应考虑其安全性、环保性和经济性。对于油基切削液,要注意防火安全;对于水基切削液,要考虑排放问题,确保符合环保要求。
总之,选用合适的切削液需要综合考虑多方面因素,以确保加工质量和效率。在实际应用中,可根据具体情况调整切削液品种和浓度,以达到最佳加工效果。