数控车床工件校正
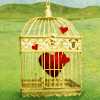
数控车床工件校正通常包括以下步骤:
1. 工件安装:首先,确保工件正确安装在车床的卡盘或夹具上。使用中心架或跟刀架来增加工件的稳定性,特别是对于长轴类工件。
2. 对刀:使用对刀棒或对刀仪进行对刀,确保刀具与工件的相对位置准确。对刀时,应根据工件的加工要求选择合适的对刀方法,如接触式对刀或非接触式对刀。
3. 初始切削:进行小范围的切削,检查刀具与工件的接触情况,确认没有干涉或偏斜现象。如果发现偏斜,需要调整刀具位置或工件夹紧。
4. 测量校正:使用游标卡尺、千分尺或三坐标测量机等工具,测量工件的尺寸和位置,与设计要求进行对比。如果发现偏差,可通过调整机床参数或工件位置进行校正。
5. 循环检查:在加工过程中,定期进行测量和校正,确保工件在整个加工过程中保持在公差范围内。如果发现偏差逐渐增大,可能需要检查刀具磨损情况,及时更换刀具。
6. 优化切削参数:根据工件材料、硬度和精度要求,调整切削速度、进给量和切削深度等参数,以提高加工精度和效率。
7. 修整刀具:定期修整刀具,保持刀具的锋利度,避免因刀具磨损导致的加工精度下降。
8. 工件清理:加工完成后,清理工件表面的切削残留物,确保工件表面光洁度。
1、数控车床工件夹紧方法
在数控车床中,工件夹紧方法的选择对工件的校正和加工精度至关重要。常见的工件夹紧方法包括:
1. 三爪卡盘:适用于圆形工件,通过旋转卡爪来夹紧工件,操作简单,但夹紧力可能不均匀,对工件的圆度有一定要求。
2. 四爪卡盘:提供更均匀的夹紧力,适用于需要高精度夹紧的工件,如轴类零件。
3. 软爪卡盘:适用于薄壁或易变形工件,通过软质材料(如橡胶)的弹性来夹紧,减少对工件的变形影响。
4. 心轴夹紧:适用于长轴类工件,通过中心架或跟刀架配合使用,提供稳定的支撑。
5. 自定心卡盘:通过卡爪的自定心特性,夹紧不同直径的工件,适用于多规格零件的加工。
6. 夹具:根据工件形状和加工要求设计专用夹具,提供精确的定位和夹紧,适用于批量生产。
选择合适的夹紧方法,结合适当的夹紧力,可以有效提高工件的校正精度和加工质量。
2、数控车床刀具选择
数控车床刀具的选择对加工精度和效率有很大影响,主要考虑以下因素:
1. 刀具材料:硬质合金刀具适用于钢和铸铁材料,高速钢刀具适用于铜和铝等软金属。根据工件材料选择合适的刀具材料。
2. 刀具类型:根据加工任务选择合适的刀具类型,如外圆车刀、端面车刀、切槽刀、螺纹刀等。
3. 刀具几何参数:刀具的前角、后角、主偏角和副偏角等几何参数会影响切削性能,需要根据工件材料、切削速度和进给量进行调整。
4. 刀具尺寸:刀具的直径和长度应与工件尺寸和加工要求相匹配,过大或过小的刀具都会影响加工效果。
5. 刀具涂层:刀具表面的涂层可以提高耐磨性和减小摩擦,如氮化钛涂层、氮化铝钛涂层等。
6. 刀具寿命:考虑刀具的耐用性和经济性,选择性价比高的刀具。
根据工件的材料、形状和加工要求,选择合适的刀具,可以提高加工精度,降低刀具磨损,提高生产效率。
通过正确的工件安装、对刀、测量校正、切削参数优化以及合理的刀具和夹紧方法选择,可以确保数控车床加工出高质量的工件。不断学习和实践,提升操作技能,是提高加工精度的关键。