一些去毛刺的方法
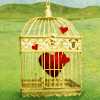
去毛刺的方法主要有机械去毛刺、化学去毛刺、电化学去毛刺、激光去毛刺和超声波去毛刺等。
1. 机械去毛刺:包括研磨、抛光和砂带打磨等方法。研磨使用磨料对工件进行切削,抛光则是利用抛光剂和抛光轮对工件表面进行精细处理,砂带打磨则是通过砂带的高速运动,对工件进行快速去毛刺。
2. 化学去毛刺:也称腐蚀去毛刺,通过化学溶液对工件的毛刺进行溶解,达到去毛刺的效果。这种方法适用于金属和塑料等材料,但需注意对工件基体的腐蚀控制。
3. 电化学去毛刺:利用电解作用,使工件毛刺在电解液中优先溶解,从而达到去毛刺的目的。这种方法适用于金属零件,特别是难以机械加工的部位。
4. 激光去毛刺:利用高能激光束对工件毛刺进行瞬间蒸发,实现无接触、无热影响区的去毛刺。适用于精密零件和复杂形状的工件。
5. 超声波去毛刺:通过超声波振动产生的机械能,使工件与磨料或清洗液之间产生强烈摩擦,去除毛刺。这种方法适用于各种材料,尤其适合微小和精密零件。
选择合适的去毛刺方法,需要考虑工件材料、毛刺的形状和尺寸、工件的精度要求以及生产成本等因素。在实际操作中,有时还需要结合多种方法,以达到最佳的去毛刺效果。
1、去毛刺的必要性
去毛刺的必要性主要体现在以下几个方面:
1. 提高产品质量:毛刺的存在会影响工件的外观质量,对于精密机械和光学仪器等对表面质量要求极高的产品,去毛刺是必不可少的步骤。
2. 保证功能性能:毛刺可能在运动部件之间产生卡滞,影响设备的正常运行,甚至导致设备故障。去毛刺可以确保设备的顺畅运行。
3. 防止损伤:毛刺尖锐,可能会在装配或使用过程中划伤操作人员或损坏其他部件,去毛刺有助于保障操作安全。
4. 延长使用寿命:毛刺会加速磨损,通过去毛刺可以减小磨损,延长工件的使用寿命。
5. 符合行业标准:许多行业对产品的表面质量有严格的规定,去毛刺是达到这些标准的必要步骤。
因此,去毛刺是制造过程中不可或缺的环节,对于确保产品质量、设备性能和用户安全具有重要意义。
2、去毛刺后的表面处理
去毛刺后的表面处理通常包括以下几个步骤:
1. 清洗:使用溶剂或清洗剂去除工件表面的残留物,如切削液、磨料、化学溶液等,确保表面清洁。
2. 抛光:对去毛刺后的表面进行抛光,提高表面光洁度,减小表面粗糙度,增强产品的外观质量。
3. 防锈处理:对于金属工件,去毛刺后可能暴露新的金属表面,容易生锈,因此需要进行防锈处理,如涂漆、电镀或磷化等。
4. 表面硬化:对于需要提高耐磨性和抗腐蚀性的工件,可以进行表面硬化处理,如渗碳、氮化、镀铬等。
5. 检测:对处理后的表面进行质量检测,确保达到设计要求和行业标准。
通过这些表面处理步骤,可以进一步提升工件的性能和使用寿命,使其满足更严格的应用需求。
去毛刺是制造工艺中不可或缺的环节,选择合适的去毛刺方法和后续的表面处理,对于提升产品质量、确保设备性能和用户安全具有重要意义。